射出成形における冷却工程は、全サイクルの中でも最も時間がかかる部分です。
この冷却時間を短縮することは、生産性や品質の向上に直結します。そこで近年注目されているのが「コンフォーマル冷却(Conformal Cooling)」という革新的な技術です。
今回の記事では、コンフォーマル冷却の仕組みや利点、設計方法、さらに導入上のデメリットや注意点までを詳しく解説します。
コンフォーマル冷却とは?
コンフォーマル冷却とは、成形品の3D形状に沿って冷却チャンネル(配管)を設計する手法です。
従来のように直線的な穴を開けて水を通すのではなく、複雑な形状に対応し、熱がこもりやすい部分にも効率的に冷却が届くようになります。
この冷却チャンネルは通常、金属3Dプリンタ(SLM/DMLS)などの積層造形技術によって製造され、これまで不可能だった形状も自由に設計できる点が大きな特徴です。
従来の冷却との違い
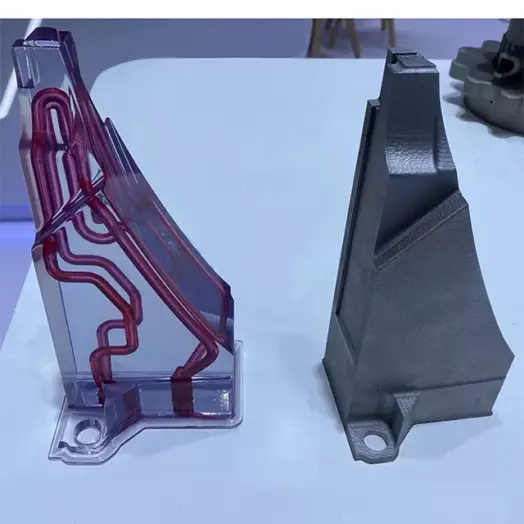
従来の冷却は、直線的にドリル加工した冷却管を使用するため
厚肉部や凹凸のある箇所では冷却が行き届かず、熱ムラが発生しやすいという課題がありました。
一方、コンフォーマル冷却では製品表面から常に等距離を保つように冷却チャンネルを配置できるため
冷却のムラを減らし、反りやヒケ、寸法不良の抑制につながります。
コンフォーマル冷却のメリット
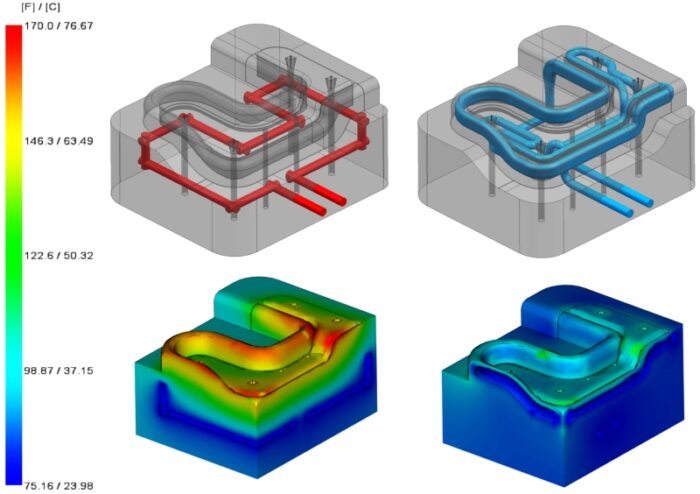
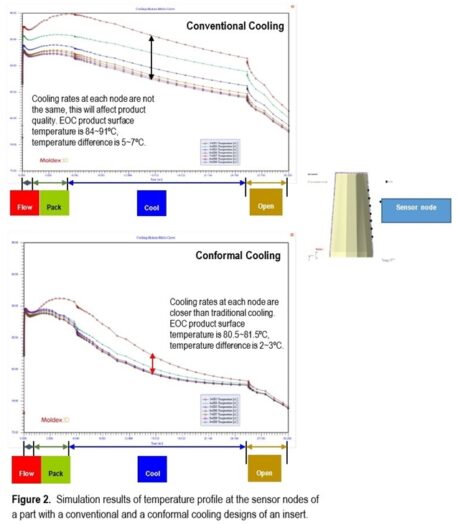
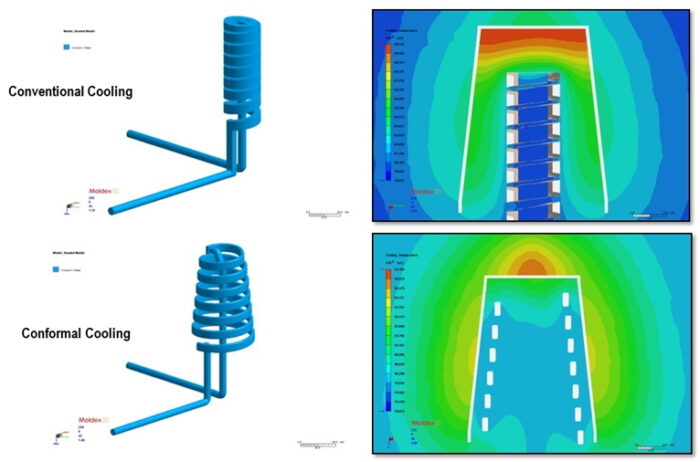
コンフォーマル冷却には、従来の冷却方式にはない多くの利点があります。
特に冷却効率の向上と成形品質の安定化という観点から、製造現場において注目されています。
以下に代表的なメリットを整理します。
- 冷却時間の短縮:冷却効率が向上し、サイクルタイムを最大30%短縮するケースもあります。
- 寸法安定性の向上:熱ムラが少ないため、製品の反りや変形を抑えやすくなります。
- 不良率の低減:焼けや変色、ヒケなどのトラブルを防ぐことができます。
- 複雑形状への対応:リブやアンダーカット近傍など、従来冷却が難しかった領域にも対応可能です。
コンフォーマル冷却は3Dプリンタなしで設計できるのか?
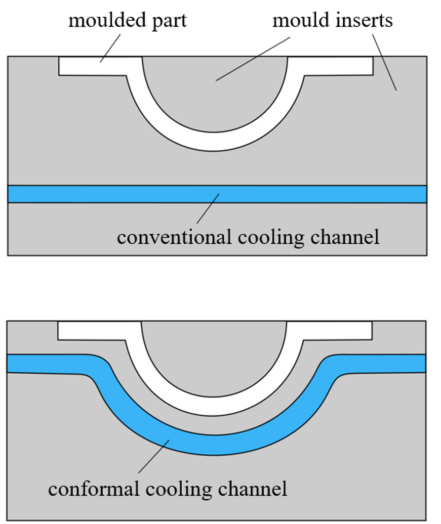
結論から言えば、3Dプリンタを使用しなくても製品形状にある程度沿った冷却チャンネルを設計することは可能です。
しかし、設計の自由度や冷却効率には限界があり、真の意味での“コンフォーマル”とは言い難い場合もあります。
以下のような代替手法が存在します。
可溶性コア(Sacrificial Core)方式
冷却経路を形成するための可溶性素材(例えば石膏や塩)を金型内に封入し、後から水などで溶かして冷却チャンネルとする方法です。
- 利点:複雑形状が可能
- 欠点:大量生産には不向き、再現性や耐久性に課題
ブロック分割・組立式金型
金型(主に入れ子)を複数の部品に分割設計し、機械加工で冷却経路を彫り込み、組み立てて冷却チャンネルを形成する方式です。
- 利点:汎用加工機で対応可能、メンテナンス性良好
- 欠点:接合部からの漏れ対策が必要、自由度は3Dプリントに劣る
電極放電加工(EDM)やガンドリルの工夫
曲線状にはできなくても、斜めドリル・段付きドリル・湾曲配置などで近似的に製品形状に沿った冷却ラインを作る手法もあります。
- 利点:一般的な加工で製作可能
- 欠点:“等距離冷却”という点では理想的でない
5軸マシニングセンタを用いた工夫
5軸制御のマシニングセンタを活用することで、あらゆる角度からの穴あけ加工や斜め方向への貫通が可能になります。
これにより、従来の3軸では難しかった曲面沿いの冷却チャンネルの形成や、干渉を避けたルーティングが可能になります。
- 利点:高精度かつ柔軟な加工が可能/バイスや治具を活用すれば既存設備で対応できる場合もある
- 欠点:加工プログラムの難易度が高く、治具設計や加工精度の確保に注意が必要3Dプリンタなしでも、工夫次第で近似的なコンフォーマル冷却を実現することは可能です。ただし、こうした手法では真の意味で製品形状にぴったり沿った「等距離冷却」は難しく、性能面では3Dプリントによる冷却チャンネルに劣る点が多いです。設計段階でどこまで性能を求めるかを明確にし、最適な製造方法を選定することが重要です。
3Dプリンタなしでも、工夫次第で近似的なコンフォーマル冷却を実現することは一応可能ではあります。
ただし、こうした手法では真の意味で製品形状にぴったり沿った「等距離冷却」は難しく、性能面では3Dプリントによる冷却チャンネルに劣る点が多いです。
設計段階でどこまで性能を求めるかを明確にし、最適な製造方法を選定することが重要です。
設計手法と使用ツール
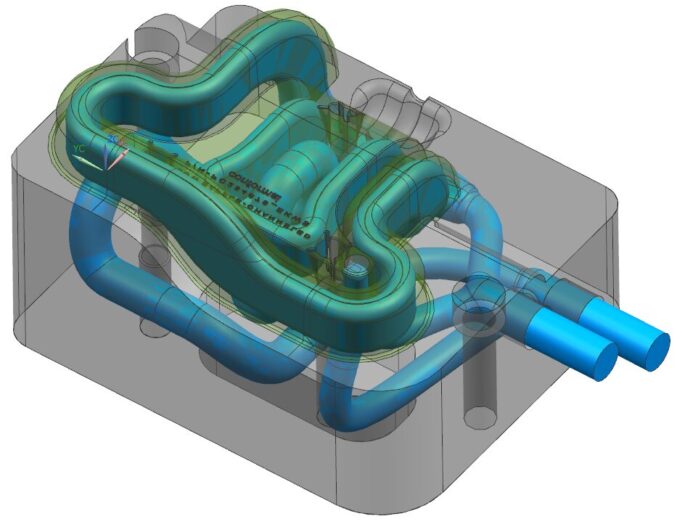
コンフォーマル冷却を効果的に導入するためには、単に冷却チャンネルを設けるだけでなく、設計段階からの綿密な計画とツールの活用が不可欠です。
ここでは、実際に使用される代表的な設計手法や支援ツールについて紹介します。
- 製品の3Dモデル化(CAD)
- 温度・流体解析(CAE)
- 等距離チャンネルの設計
- 金属3DプリンタやMIMによる造形
また、コンフォーマル冷却の設計に適したCADソフトも存在します。たとえば以下のようなツールが代表的です。
- Autodesk Fusion 360
クラウドベースで設計・シミュレーション・CAMを統合。スカルプト機能を用いて複雑な冷却チャンネルも設計可能です。 - Siemens NX(Conformal Cooling Extension)
専用モジュールを利用することで、金型内の等距離冷却チャンネルを自動で生成できます。MoldflowやSimcenterとの連携も強力です。 - PTC Creo + Mold Design Extension(MDX)
冷却チャンネルの設計と流体シミュレーションを一体化して行えます。多段構造や複雑形状にも対応可能。 - Autodesk Moldflow Insight / Adviser
冷却性能のシミュレーションに特化。コンフォーマル冷却設計と結果の可視化が可能で、冷却効果や変形リスクを数値で把握できます。 - SOLIDWORKS(with Mold Tools / Flow Simulation)
SOLIDWORKSのモールドツールやFlow Simulationを活用すれば、金型設計における冷却チャンネル設計および熱解析が可能です。複雑な流路もCAD上で自由に設計でき、外部ソフトと連携することなく一貫した設計環境が構築できます。
これらのツールを活用することで、設計の効率化と品質向上の両立が期待できます。
特にCAEと連携したツールを使えば、最適な冷却設計を科学的根拠に基づいて実現することが可能です。
コンフォーマル冷却のデメリット・課題
コンフォーマル冷却は非常に魅力的な技術ですが、導入にあたっては注意すべき点も多く存在します。
特に製造コストや設計の複雑さ、メンテナンス性など、従来の金型と比べた際の明確な課題がいくつかあります。
ここでは、代表的なデメリットとその背景について詳しく見ていきます。
製造コストの増加
金属3Dプリンタによる製造が前提となるため、金型の初期コストが高額になります。小ロットや試作には不向きで、量産向けの金型に限定されることが多いです。
材料強度と耐久性の問題
SLMで製造された金型部品は、従来の鍛造材と比べて微細な気孔(ポロシティ)が残ることがあります。これにより、疲労特性やクラック耐性に影響を与える可能性があります。ただし、適切な熱処理(例:18Ni300鋼で560℃×8時間)を施すことで、HRC48以上の強度を得られるという研究もあります。
設計・解析の負荷
冷却チャンネルの設計には高度なCAE解析と最適化が必要です。設計担当者には、熱流体解析や応力解析の知識が求められ、設計期間も通常より長くなる傾向があります。
流体制御とメンテナンス性
複雑な流路形状は水流抵抗や流量の不均一を引き起こす可能性があります。さらに、冷却チャンネルが詰まった場合の再加工や清掃は困難です。
適用判断のポイント
コンフォーマル冷却は万能ではありません。コストや設計工数を考慮すれば、すべての金型に向いているとは限らないからです。
ここでは、どんな製品や生産条件において導入する価値が高いのかを、簡単に整理してみましょう。
条件 | コンフォーマル冷却の適性 |
---|---|
製品が厚肉・反りやすい | ◎ 非常に効果的 |
年間生産数が多い(10万個〜) | ◎ コスト回収可能 |
高精度が求められる(自動車・医療) | ◎ 品質重視なら導入価値あり |
少量生産・頻繁な設計変更 | △ 投資対効果が見込めないことも |
まとめ
コンフォーマル冷却は、冷却効率と品質の両方を高められる、まさに次世代の金型冷却技術です。
製品の形に合わせてチャンネルを設計することで、成形サイクルを短くし、不良も減らせて、寸法の安定性まで向上する――そんな嬉しいメリットがそろっています。
ただし、導入にはそれなりのハードルもあります。
3DプリンタやCAEの設備、そしてそれを使いこなす知識やスキルが必要です。「なんとなく良さそう」で入れるには少し重たい技術かもしれません。
だからこそ、どの製品にどれだけの効果があるのか、しっかりと見極めてから導入を検討することが大切です。
今後、材料技術や製造手法の進化が進めば、もっと多くの現場で当たり前のように使われる日も近いかもしれませんね。
リアクション投稿