ヒケが起こる原因と対策
ヒケが発生する場所といえば、主に肉厚の部分です。
ヒケというのは製品表面に出る凹みのことを指すのですが、なぜヒケが起こるのか?
これは樹脂が収縮することと関係しており、製品の厚みがある部分ほど内部への冷却が遅れます。均一に固化されるには肉厚が均等であることが理想ですが、ところどころ厚みが変わってしまうとそれぞれで収縮が早い部分と遅い部分が出ることにより、肉厚の部分だけ内側への収縮がより進んでしまうためです。
よって、同じ製品を成形した場合でも、ABSなど収縮率の小さな樹脂よりもPPなどの収縮率の大きな樹脂のほうがヒケがより目立ちやすくなります。
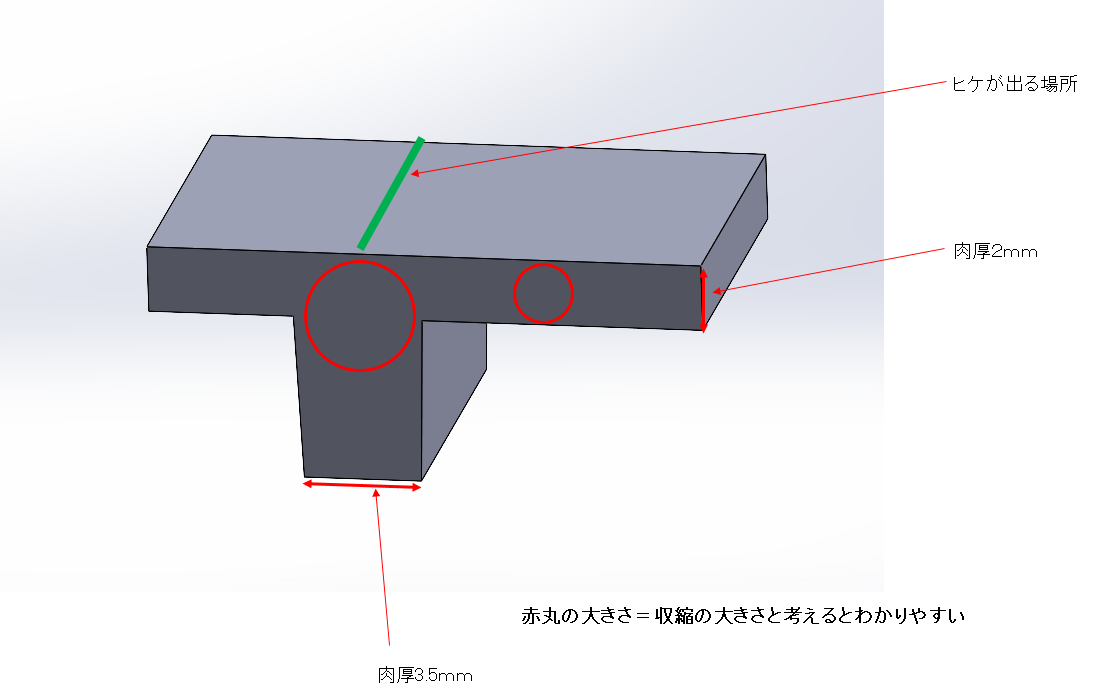
イメージです。製品リブ部の断面。製品の肉厚が2mm、リブ部先端が3.5mm。
上の図は製品肉厚2mmに対して3.5mmのリブが立っているという製品の断面を表したものですが、リブ部の赤丸部と製品肉厚部の赤丸部の大きさが明らかに違うのがわかると思います。大きな赤丸部であるリブ部のほうが、より大きく収縮することで製品が内側に凹み、表面にヒケをつくってしまうというわけです。
ヒケの対策
成形時での対策であれば
- 低い温度でなるべく圧力を高く充填して収縮を小さくする
- 金型の温度を80~100℃辺りに高くしておく
等が考えられます。
しかし、事前にそのようなトラブルをさけるためには、元々の製品の設計段階からなるべくヒケを作らないようなモデルにしておくのが得策ですね。
上述したリブが厚いという場合は極力リブを薄くすれば、それだけヒケの影響も出にくくなります。
(しかし薄くすればまったくヒケがでなくなるというわけではありません)
ボスがある場合も同様、ボスの部分が肉厚にならないよう、それが可動にある場合は、
固定から均等肉厚になるような肉盗みを設けるなどの設計変更が必要な場合があります。
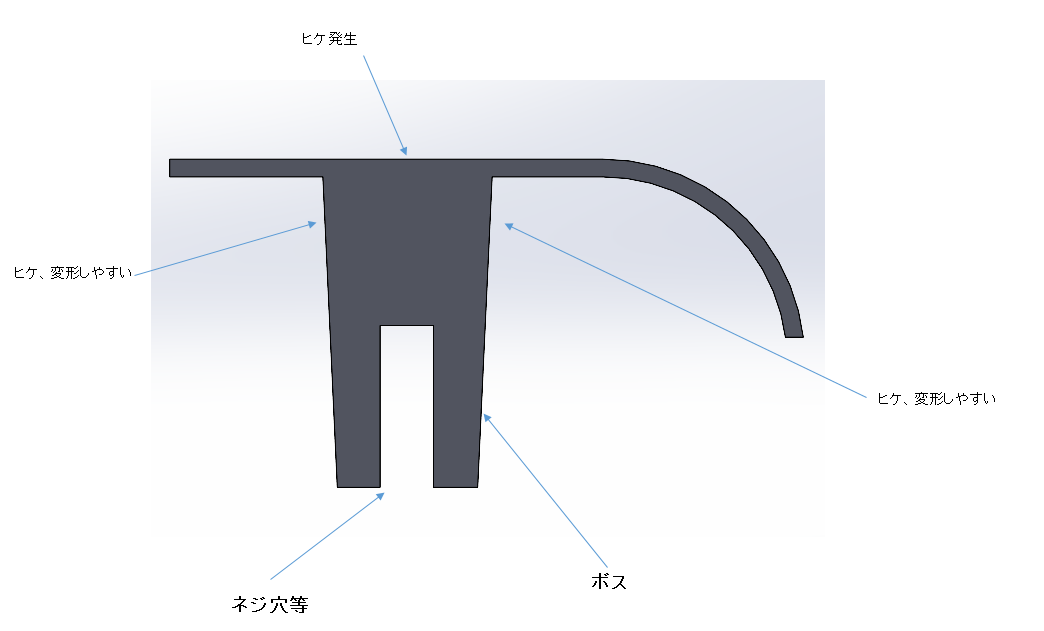
ボスの根本と、表面にヒケが出ます
上の図はボス部の断面。
ネジ穴となる部分は良いのですが、その上が肉厚になってしまっている場合、ボスの根本と製品表面にヒケが出てしまいますので、肉盗みを設けるなど対策が必要です。
また、ボス根元の変形により、穴の位置が図面交差を外れるほど極端に変わることはないにしても、収縮によって製品のボスの高さが変わる可能性は考えられます。
鏡面の場合はより目立つがシボでは目立ちにくい
製品の表面が鏡面の場合、成形品に映る光の歪みなどもあり、ヒケはより目立ってしまいます。
しかし、逆に表面が荒いものの場合は目立ちにくくなるため、シボをいれるとヒケが目立たなくなります。
許容範囲内でのことですが、あえて磨かない、また荒めで仕上げるなどの磨き調整でヒケの見え方を変えることも対策になります。
まとめ
まとめです。
- 設計の段階で、リブの厚みや極端な肉厚部等ヒケが出るであろう部分をチェックしておく
- ヒケ防止対策としてはリブを細くする、肉盗みを設けるなどの対策である程度は可能
- 面の荒さ次第ではヒケをある程度目立たなくさせることは可能
- 鏡面仕上げの製品の場合は少しのヒケでも目立ってしまう
- シボ加工をした場合は、製品表面のヒケを目立たなくさせることが可能
ということで、今回はプラスチック金型製品のヒケの原因と対策の初歩についてでした。
関連記事
リアクション投稿
コメント一覧 (1件)
[…] 射出成型金型の製品にヒケが起こる原因と対策の初歩 […]