「ピンゲートに捨て板を設置する例」
非常に小さな製品を直接ピンゲートで入れてしまうと、樹脂が入り過ぎて成形がうまくいかない可能性があります。
小さな製品とは、どの程度の大きさかというと、例えば大体直径10mm~18mm位、高さが10mm~18mm位の指でつまめる程度の大きさのものです。
1個取りや2個取りで、ほんの少しの距離のランナーを通るくらいでは、成形機の各設定が最低であっても一瞬で樹脂が入りきってしまうことで、良品が取れない可能性があります。
良品が取れないと思われる主な理由は、例えば樹脂が一瞬で入ってしまうことによって樹脂圧で型が浮く、つまりPLやそこに設けたスライドが開いてバリができやすくなる、また内部歪、残留応力が生じるなどです。
タブゲートと目的は同じ?タブゲートの例
というわけで、一気に樹脂が入ってしまうのを防ぐために、一度樹脂の勢いを逃がす&樹脂の通る距離を長くするという目的で、ランナーの途中に捨て板を設けるという方法をとります。これはタブゲートの目的と同じようなものかもしれません。
ちなみにタブゲートについては👇
タブゲートは流動性の悪い樹脂に有効であり、ジェッティングやフローマークの防止、またゲート付近の残留応力防止にも効果があります。
タブゲートの形状としましてはランナーの途中で一度ランナーを絞る形(串にささった団子?のようなイメージ)で、再びランナーの大きさに戻して最終的にランド→製品へという感じになります。
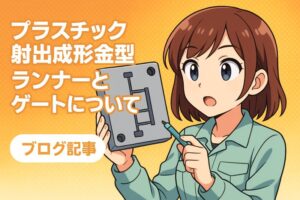
タブゲートが流動性の悪い樹脂に有効~というと、樹脂が一気に入り過ぎてしまう今回の場合と矛盾してるように思われますが、元々は流動性が悪いから成形時に射出圧力を高くしなければならず、そうなるとゲート部に歪みが生じやすくなるので、その歪みを緩和させる、というのがタブゲートの目的。
つまり、今回の場合の「樹脂圧を抑えるためにゲートに捨て板というワンクッションを設けて緩和させ、樹脂を製品部へとじんわりと入れる」というイメージと共通しているのではないかと思います。
ちなみにタブゲートにも様々な形がありますが、弊社がサイドゲートの際にジェッティングやフローマークの防止に役立ったのが以下のようなゲート形状です。
ゲートの絞りは二段階に設けることもあります。
では、本題に戻ります。
ピンゲートの際に捨て板を設置するというのは、例えばこのようなイメージ👇です。
樹脂が流れる順番は1,2,3の順で、捨て板を経由して製品へ樹脂が流れていくことになります。
板の厚みは2~3mm程度と薄めです。
注意しなければならないのは、捨て板が固定ベース側に大変とられやすくなりますので、捨て板側面の勾配はランナーと同じ程度ではなく、20度くらいはとったほうが良いでしょう。(そもそも板の形状は四隅も底も角じゃなく、Rで良い)
また、それでもまだ固定側にとられそうであれば、捨て板のどこかにランナーロックピンを設けると良いでしょう。
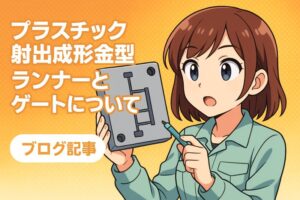
まとめ
モノにもよれば、取り数や樹脂にもよると思いますので、小さな製品すべてに当てはまるものではないでしょう。
しかし、取り数が1個や2個の場合は、検討する必要はありそうです。なぜなら、1個取りや2個取りだと、設計時にスプール付近に製品を設置して、樹脂がほぼほぼ直接入ってしまう型構造にしてしまいがちだからです。(スプール→ほんのちょっとランナーがあって、すぐにゲートのような設計)こういった場合は捨て板を設けるとか、ランナーをわざと長くする(途中で調整ピンも設ける)、製品を所定の位置よりも離す等々考えた方が良いかもしれません。
リアクション投稿
コメント一覧 (2件)
[…] 関連記事小さな製品のピンゲートは直接だと樹脂が入り過ぎるため、ランナーに捨て板を設けるとうまくいく【タブゲートについて】 […]
[…] 関連記事小さな製品のピンゲートは直接だと樹脂が入り過ぎるため、ランナーに捨て板を設けるとうまくいく【タブゲートについて】 […]