ヒケ(SinkMark)とは?
ヒケとは「充填された樹脂が冷却の不均一により体積の収縮差を生じ、表面がくぼんだ状態になること」である。
射出成形の工程では、金型の一部に樹脂を固めるのに十分な圧力がかからないことがある。そうすると、プラスチックが収縮する速度が他の部分より遅いその部分に、さらに応力がかかることがある。このストレスによってプラスチックの表面が引っ張られ、固まりきっていないためにヒケが発生する。
NexPCB より引用
ちなみに「ヒケ」は英語で「Sinkmark」といいます。その他射出成型で使う英語については以下のページにまとめています。
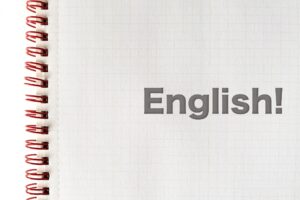
ヒケが起こる要因・成形条件
- 射出圧力・保持圧力が低い
- 射出・保圧時間が短い
- 冷却時間が不足している
- 成形温度が高い(冷却固化収縮が大)
- 金型温度の高すぎ、または低すぎ
- クッションがゼロ
成形条件によるヒケの対策
- 射出圧力・保持圧力を高める
- 射出・保圧時間を長くする
- 冷却時間を充分とる
- シリンダー温度を下げる
- 金型温度を適正にする
- クッションを5~10mmとる
ゲート付近でヒケが発生した場合は、保持時間を長くすることで解決できることがあります。
表面が肉厚で凹んでいる場合は、金型内製品部の冷却時間を延長する必要があります。
入子の周囲に溶融物の部分的な収縮による陥没やヒケがある場合、これは主に入子の温度が低いことが原因なので、入子の温度を高くするようにします。
また、ヒケの原因が送り不足によるものであれば、送り量を増やす必要があり、金型を十分に冷却する必要があります。
金型・設計の場合
続いて、金型設計での要因と対策について
画像引用 goengineer How to Minimize Sink Marks in Ribs in SOLIDWORKS Plastics
金型によるヒケの要因
- 肉厚が厚い
- ランナー・ゲートが小さい
- ゲート位置の不良
- 冷却回路が不十分
金型によるヒケの対策
- ランナー・ゲートを大きくする
- 肉厚に変化のある成形品の場合、厚肉部にゲートをつける
- 肉厚を可能な限り均等、または薄くする(周囲の肉厚差をなくす)
- 肉厚部の角にRを設けて肉厚変化を緩やかに変更する
- 肉盗みやリブを設ける
- 冷却回路の見直し
このほか、金型コア側に新たに冷却配管などを設けたり、予算が許されるのであれば、金型を熱伝導性の高いベリリウム銅で作成するのも手です。(ベリリウムは銅とは比べ物にならないほど高価で、切削性が悪く、工具が食いつきやすい。タッピングは非常に折れやすいので通常の下穴径よりも0.3~0.4mmは大きな穴をあけたほうが良い)
ヒケまとめ
射出圧力と射出速度を適切に上げ、溶融物の圧縮密度を高め、射出と保圧の時間を長くし、溶融物の収縮を補い、射出バッファーの容積を大きくする。
ただし、保圧は高すぎると凸凹の原因になるので、高すぎるのはダメ。
ゲート付近にへこみやヒケが発生した場合は、保圧時間を長くすることで解決します。
製品部に肉厚の凹みがある場合は、金型内のプラスチック部品の冷却時間を適切に延長する必要があります。
インサート周辺のへこみやヒケは、溶融物の部分的な収縮が原因である場合、これは主にインサートの温度が低すぎることが原因ですので、インサートの温度を上げると良い結果となる場合があります。
材料の供給が不十分で製品部の表面が陥没している場合は、材料の供給量を増やす必要があり、また金型内製品部の冷却が十分であることが重要です。
表面への要求が高い製品には、できるだけ収縮特性の低い樹脂を使用する必要があります。(収縮率の高い樹脂ほどヒケが出やすい)
「成形機に逆流防止機構をつける」も対策のひとつ
過去関連記事
リアクション投稿
コメント一覧 (2件)
[…] ヒケが発生する成形、金型両方から見た要因と対策(sink mark) […]
[…] […]