はじめに
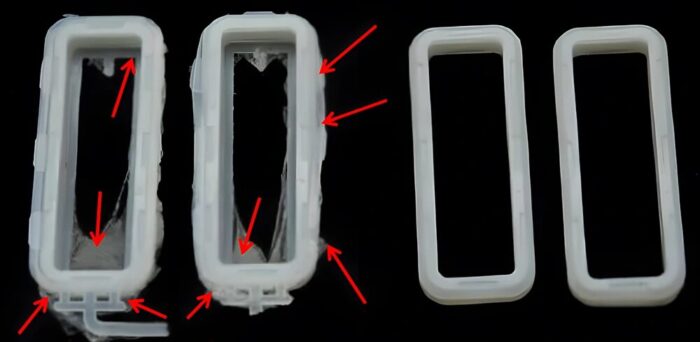
バリというのは、射出成形の製品にできる“はみ出し樹脂”のことで、金型の合わせ目(パーティングライン)や部品の隙間から、余分な樹脂が薄く出てしまったものを指します。
たいていは製品のフチや型の境目に沿ってできやすく、エジェクタピンの周辺やインサート部品の合わせ部分なんかにもよく見られます。バリ自体はすごく薄いので目立たないこともありますが、見た目が悪くなったり、寸法がズレたりして、組み立てのときにうまくハマらない原因になることもあります。
そのため、成形後には「バリ取り(トリミング)」と呼ばれる処理が必要になるのですが、これがなかなか手間で、コストもかかります。結果として、生産効率が落ちたり、品質にばらつきが出たりするリスクも出てきます。完全にバリをなくすのは難しいですが、なるべく出ないように工夫することが、成形工程では大事なポイントになります。
バリ発生のメカニズム
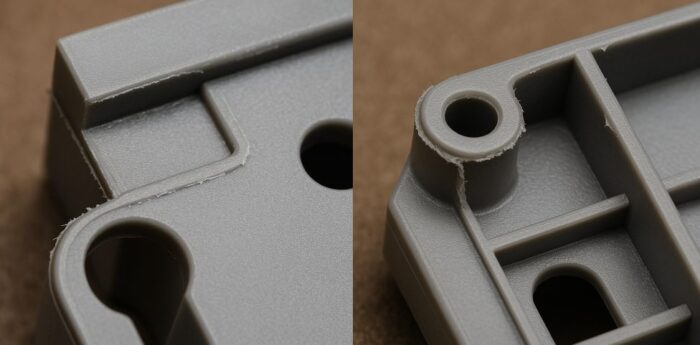
バリは、射出成形中に溶けた樹脂が金型の合わせ目や、わずかな隙間(クリアランス)に流れ込んで外に漏れ出すことで発生します。
本来、成形時には金型の雄型と雌型が強い型締め力でピッタリ閉じていて、樹脂が漏れないようになっています。でも、いろいろな要因でわずかなスキマができてしまったり、樹脂が勢いよく流れすぎたりすると、どうしても弱い部分から樹脂が押し出されて、薄い膜のように固まってしまうんです。それがバリです。
このバリを放っておくと、次第に型の合わせ面に入り込んで「かじり(かしり)」と呼ばれる金型の損傷を起こしたり、次に作る製品でもバリがどんどん大きくなってしまうという悪循環にハマります。だからこそ、バリが出始めたら早めに原因を見つけて、しっかり対策を打つことがとても大切なんです。
バリの主な原因
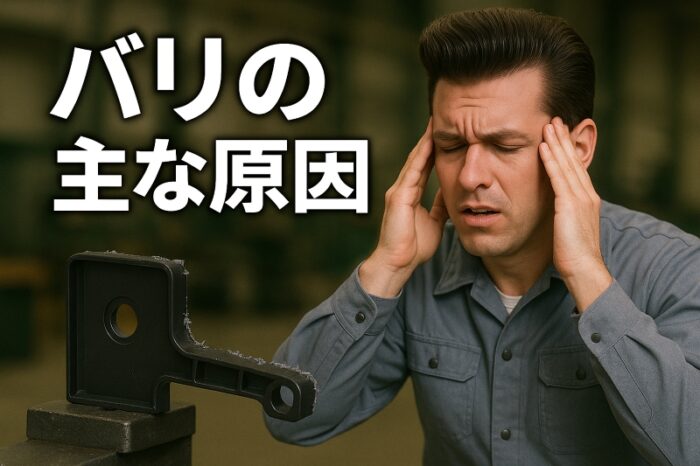
型締め力不足と金型閉鎖不良
射出成形中に型締め力が足りないと、金型が圧力に負けて少し開いてしまい、合わせ目から樹脂が漏れ出してバリの原因になります。
とくに気をつけたいのが、射出後の「パッキング」や「保圧」といった工程。ここでは中の圧力がさらに上がるので、型締めが弱いと、その圧力で型がわずかに開いてしまい、バリが出やすくなるんです。
さらに、型締め装置に問題がある場合――たとえば、トグル機構の調整がうまくいっていなかったり、タイバーの張力が左右でバラバラだったりすると、金型がちゃんと密着しないことがあります。そうなると、一部にだけスキマができて、そこから樹脂が漏れ、片側だけにバリが出る、なんてことも起こります。
改善策
●適切な型締めトン数を確保する
まずは、今使っている成形機の型締め力が、製品のサイズと樹脂の圧力に見合っているかをチェックしましょう。もし型締め力が足りていなければ、より大型の成形機を使うか、設定を見直して型をしっかり締める必要があります。
目安としては、「製品+ランナーの投影面積 × 材料ごとの推奨圧力(トン/cm²など)」で必要な型締め力を計算できます。十分なトン数があれば、射出時の内圧に負けず、バリの発生を防ぐことができます。
●成形条件を見直す
射出圧力や保圧が高すぎると、それだけで型が開こうとする力が大きくなります。設定を見直して、必要最小限の圧力に抑えることで、型開きによるバリを防げる場合があります(このあたりは後述の「射出圧力の過多」も参照ください)。
●金型の取り付けと成形機の整備も重要
金型がちゃんと水平に、ズレなく取り付けられているかも要チェックです。トグル機構や油圧装置にガタつきや摩耗があると、型全体に均等な締め付け力がかからず、どこかにスキマができてバリが出やすくなります。金型とプラテンの間に異物が挟まっていないか、取付けボルトの緩みがないかなども忘れず点検しましょう。
●ショートショットで発生タイミングを見極める
バリがいつ出ているのかを確かめるには、ショートショットを試してみるのが有効です。これは、射出の第一段階であえて途中までしか充填せず、その時点でバリが出ているかどうかを見る方法です。
ショートショットではバリが出ないのに、完全に充填したときだけ出る場合は、保圧や充填後半で型締めが負けている可能性が高いです。この場合は保圧条件の見直しや、型締めトン数の強化が必要になります。
型締め力が強すぎるのも逆効果になることがあります。
型締め力は強ければ安心…と思いがちですが、実は“強すぎる”のも問題です。必要以上に強く締めすぎると、金型のベント(空気抜きのための隙間)を潰してしまって、ガスが逃げにくくなります。その結果、ガス焼けや型内圧の異常、最悪の場合は型の損傷にもつながる恐れがあります。
また、過剰な型締めによって固定ベースや可動ベースがわずかに歪んでしまい、それが原因で型の中央部から徐々にバリが出てくるケースもあります。
つまり、型締め力は「とりあえず最大でOK」ではなく、製品や成形条件に合わせて適切なトン数を見極めることが、長期的に品質を安定させるうえでも重要なんです。
金型の摩耗・パーティングラインの不良
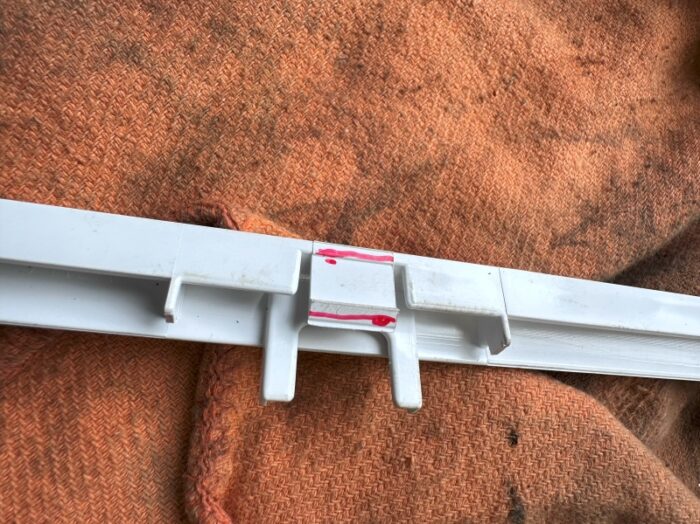
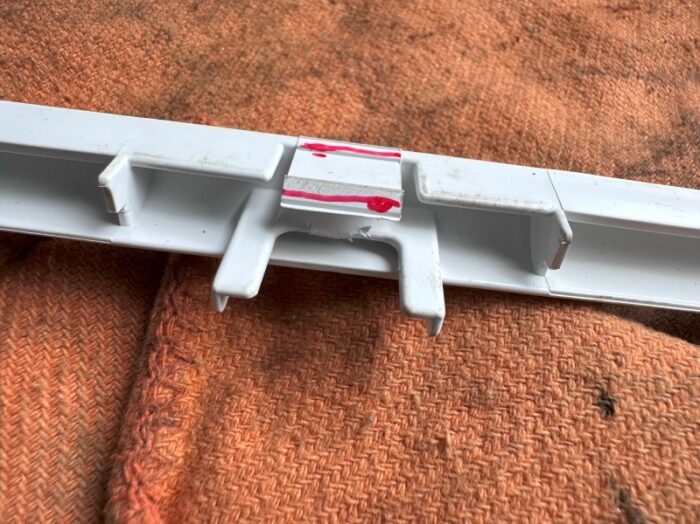
金型の“密閉性の低下”も、バリの大きな原因です。
新品の金型では、型の合わせ面(パーティングライン)がピタッと密着していて問題がなくても、成形を何度も繰り返していくうちに、少しずつ圧力による変形や摩耗が蓄積して、わずかなスキマができてしまうことがあります。
特に使い込んだ古い金型では、過去に出たバリが型に食い込んでしまい、型の表面に凹み(圧痕)をつくってしまうことがあります。そうなると、そこがさらに沈んで、バリが出やすくなるという悪循環に陥ってしまうんです。
また、金型の組み立て精度が悪かったり、そもそもパーティングラインの加工精度が甘かったりすると、雄型と雌型が完全に合わず、周囲に微妙なスキマができてしまいます。そのスキマから、やはり樹脂が漏れてバリが発生します。(そもそもそんなにスキマの多い金型ってどうなの?って話ですが……)
さらに見落としがちなのが、成形中に入り込む削りカスやホコリ、前回のショットから残っていた樹脂片などの“異物”です。こうした異物が型の合わせ面に挟まると、わずかな段差ができて、それがバリの原因になることもあります。
改善策
●金型の定期清掃は基本中の基本
パーティングラインやスライド部、リーダーピン・ブッシュ周辺などに、樹脂カスや異物がたまっていないか、成形の合間や保全のタイミングでしっかり清掃しましょう。特に、薄いバリが出ていたような場合、そのバリの破片が型に挟まり、さらにスキマを広げてしまうことがあります。清掃時には、型面に傷や摩耗がないかもあわせてチェックすると安心です。
●金型の点検・補修で密着性をキープ
長年使って摩耗してしまった金型は、専門業者によるオーバーホールや、肉盛り・再研磨などでしっかりメンテナンスしておきましょう。型締め面にへこみがあれば、平面研磨で修正します。軽いスキマであればシム(薄板)を挟んで調整する方法もあります。また、キャビティやコアに欠けや割れがあると、そこからバリが出る原因になるので、必要に応じてパーツ交換も検討しましょう。
●スポッティングで型合わせのズレを見抜く
金型を組んだら、「スポッティング」という合わせ作業で、雄型・雌型がきちんと当たっているかをチェックします。ブルーインクやレッドインクなどを使って、どこに隙間があるのか一目で分かるようにします。インクのつき方で面合わせの不具合が見つかったら、そこを仕上げ直して、樹脂が漏れないようにしっかり対策します。目に見えないわずかな段差もこの方法なら見つけられます。
●金型自体の剛性アップも選択肢
射出時の圧力で金型がたわんでスキマができてしまう場合は、金型の構造自体を補強する必要があります。型板を厚くしたり、支持柱(ピラー)を追加・太くしたりして、全体の強度を高める方法が有効です。また、型締め時に圧力が均一にかかるように、キャビティ周辺には十分なランド幅(シールオフ面)を確保しておくことも大切です。ランドが狭すぎると圧力が一部に集中して、そこがへこんでしまいやすくなります。
●型の平行度はバリ対策の要
上下型がピッタリ平行に合っていないと、どこかにスキマができてバリの温床になります。型の据え付け時には、しっかり平行が出ているか確認しましょう。タイバー(基板)の張力バランスも重要で、工場の規定値に合わせて調整しておくことが、全体の均一な型締めにつながります。大型や複雑な金型では「型のたわみ」も起きやすいので、必要に応じてサポート金具や補強フレームの追加も検討しましょう。
ガスベント不良(通気不足)
ベント(ガス抜き)の不良もバリの原因になります。
射出成形では、溶けた樹脂を型に流し込むとき、キャビティの中には当然ながら空気が残っています。この空気をうまく逃がしてやらないと、樹脂が流れ込むスペースが足りず、樹脂を無理やり押し込むような状態になります。その結果、通常よりも高い圧力が必要になり、型がわずかに開いてしまってバリが出やすくなります。
金型にはこの空気を逃がすための「ベント溝(ガス抜き溝)」が設けられていますが、これが浅すぎたり狭すぎたりすると、十分に空気が抜けません。逆に広すぎると、今度は樹脂まで漏れ出してしまい、そこからバリが発生する原因になります。
つまりベントは、「空気は通して、樹脂は通さない」という絶妙なクリアランスが必要なんです。
さらに、使う材料によっても適したベントの深さや数が変わってきます。設計がその材料に合っていないと、うまく空気が逃げずにバリの原因になることも。しかも成形を繰り返していくと、ベント溝に樹脂カスが詰まって通気が悪くなるケースもあります。最初は問題なかったのに、ある日突然バリが出始める…なんてときは、このベント詰まりが犯人かもしれません。
定期的な清掃や、材料変更時のベント設計の見直しも、バリ対策としてとても大切です。
改善策
●使う樹脂に合ったベント設計をする
ベント溝の深さや幅は、使う材料の特性に応じてしっかり調整する必要があります。たとえば、ABSなど粘度が高めの樹脂(ちょっと固めのやつ)は、多少ベントが深くても樹脂が漏れにくいですが、PPなど流動性の高い柔らかめの樹脂だと、深すぎるとすぐに漏れてバリになってしまいます。
ABSやPPなど、材料ごとに“ちょうどいい”ベント寸法は違うので※、素材を変更したときは、金型側のベント寸法も見直すようにしましょう。樹脂メーカーが出している推奨値があれば、それを目安に、必要に応じて既存の金型に再加工をかけることも大事です。※ABSだと0.05まで、PPだと0.03まで
●ベントの数と配置も重要
バリを恐れてベントの数を減らしすぎると、今度は空気が逃げられなくなって、ショートショットや焼けといった別のトラブルを引き起こします。できる範囲で、各キャビティの端っこや広い面積のところに、適切な間隔でベントを配置するようにしましょう。
目安としては、数cmおきにベントを入れるのが一般的です。形状が複雑で空気が溜まりやすそうな場所には、細いピンベントや焼き抜きピンを使ったり、最近では焼結多孔質材のベンチングインサートなんかも活用されています。
●ベントの清掃とメンテナンスは定期的に
ベント溝も使い続けるうちに、樹脂カスやガスの分解物がたまって通気が悪くなります。量産中に急にバリが出始めた場合は、まずベントが詰まっていないか疑ってみましょう。金型を分解して、スクレーパーや真鍮ブラシなどで溝をしっかり清掃してあげれば、改善するケースも多いです。
それから、型締め力が強すぎてベントが潰れていないかも要チェックです(このあたりは前述の「型締め力過多」のところも参考に)。
●射出条件とのバランスも大切
どんなにベントを良くしても、射出スピードが速すぎたり圧力が高すぎたりすると、空気が逃げきれずに圧縮されて、結局バリの原因になります。
ベントの改善とセットで、射出速度を少し落としたり、できれば真空脱泡や減圧成形といったエア対策を導入するのも効果的です。条件設定とベントのバランスをとることが、安定した成形には欠かせません。
射出圧力・速度の過多
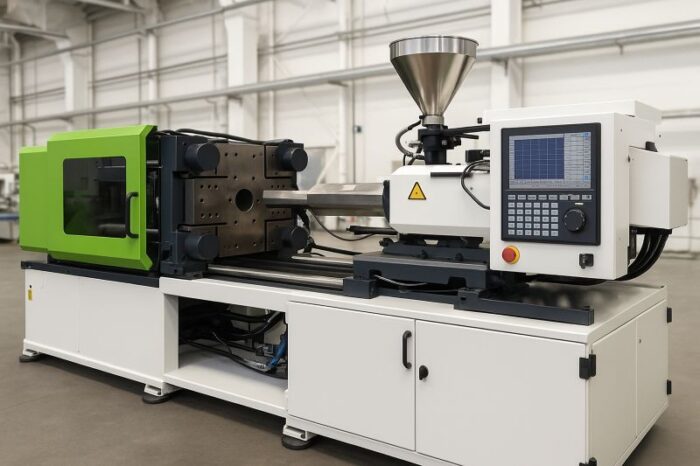
射出圧力や速度が高すぎると、バリの大きな原因になることも。
射出成形では、圧力や速度の設定が強すぎると、型の中で樹脂がものすごい勢いで流れ込んで、内部の圧力が一気に高まります。たとえ型締め力が十分あっても、その急激な圧力に耐えられず、型の合わせ面の“ちょっとでも弱い部分”がこじ開けられて、そこからバリが出てしまうんです。
特に注意したいのは、充填の終盤やパッキング工程。ここで必要以上に圧力をかけると、型が押し広げられてバリが発生しやすくなります。実際、バリが出る最大の要因はこの「かけすぎた保圧」だった、なんてケースも少なくありません。
また、射出速度が速すぎると、樹脂が型の中に“ぶつかるように”流れ込んでくるので、ウォーターハンマー的な圧力衝撃が発生し、型を一瞬広げてしまうことがあります。業界ではよく「流れの速い低粘度樹脂を叩きつけるように入れると、バリが出やすい」とも言われていますが、まさにこの現象です。
つまり、射出圧力や速度は「とにかく速く・強く」すればいいわけではなく、金型の構造や材料に合わせて、バランス良く設定していくことがとても重要なんです。
改善策
●射出速度を見直して、バリを抑える
バリ対策として、まず手をつけやすいのが「射出速度の調整」です。
充填の初期はある程度スピードが必要ですが、型がほぼいっぱいになる終盤では、スピードを落として、樹脂がやさしく流れ込むようにします。これだけで、型内の圧力や温度の急上昇が抑えられ、バリの発生リスクをグッと減らせるんです。
実際、バリが出始めたときに多くの成形技術者がまずやるのが「射出速度を落として様子を見る」こと。
射出速度は、圧力・温度・空気の圧縮状態など、いろんな要素に関係してくるので、最初の調整ポイントとしてとても効果的です。
●射出圧力・保圧を必要最小限にする
成形条件が「なんとなく高め設定」になっていないか、一度見直してみましょう。
射出圧力や保圧(パッキング)が必要以上に高いと、型内のピーク圧力が無駄に上がってバリを招くことがあります。
特に保圧については、ゲートが固まるまでの“必要な時間と最低限の圧力”だけで十分。
それ以上長く・強くかけても、製品の仕上がりは変わらず、むしろ型が開いてバリが出やすくなってしまいます。
●多段射出や圧力制御機能の活用
最近の成形機では、圧力の上がり方をモニタリングして、射出速度を自動で調整する機能(たとえば「デコッピング制御」など)も搭載されています。
こういった機能を使えば、型締め力とのバランスを自動で保ちながら射出できるので、バリ発生のリスクをより確実にコントロールできます。
●その他の成形条件もチェックしておく
圧力や速度だけじゃなく、他の条件もバリに影響することがあります。
たとえば、金型の温度が低すぎると、樹脂が途中で固まって流れにくくなり、余計に圧力がかかってしまう場合もあります。
このときは、型温を適正範囲まで上げてやると、樹脂がスムーズに流れて圧力が下がり、バリを防げるケースもあります。
また、冷却時間が短すぎると、型開き直後に製品にストレス(残留応力)がかかって変形することもあります。これは直接バリには関係しませんが、製品の歪みが型合わせに影響することもあるので、最終的な品質には無関係ではありません。
適切な冷却を取ることで、歪みを防ぎ、型面との密着性も保たれます。
樹脂の粘度・温度要因
●樹脂が“サラサラすぎる”と、バリの原因に
使っている樹脂の粘度が低すぎる、つまり“サラサラ状態”だと、金型のほんのわずかな隙間にも入り込みやすくなり、バリが発生しやすくなります。
この粘度は、射出時の温度設定や添加剤の影響で変わってきます。
たとえば、シリンダーやノズルの温度が高すぎると、樹脂が溶けすぎて粘度が下がり、通常は入らないような極小のすき間までスルッと入り込んでバリになることがあります。
実際、バレルの温度を少し下げただけで、バリがピタッと止まった…なんて例もよくあります。
●樹脂の劣化や水分にも注意
ABSやPA(ナイロン)などの吸湿性のある材料は、乾燥が不十分だと、成形時の熱で分解が進んで粘度が下がってしまい、これまたバリの原因になります。
「乾燥がちょっと甘かっただけで、バリが出まくった」というのはよくある話です。
●材料による“バリやすさ”の違い
PPやPEのような半結晶性の樹脂は、もともと流動性が高くて粘度も低め。そのぶん、ちょっとした隙間からでもすぐにバリが出やすい傾向があります。
一方、ABSは中程度の粘度なので、PPほどはバリになりにくいですが、それでも高温で使ったり、水分を含んだままだと粘度が落ちてバリの原因になります。
つまり、「材料の種類+温度+乾燥状態」の組み合わせで粘度が大きく変わり、それがそのままバリの出やすさに直結する、というわけです。
材料ごとの特性を理解して、それに合った温度管理と乾燥処理をしておくことが、バリ防止にはとても大事なんです。
改善策
●射出温度は“高すぎず低すぎず”が基本
まず大事なのは、樹脂メーカーが指定しているシリンダー温度の範囲内で成形すること。
ABSやPPなんかは、温度が低すぎると樹脂が流れにくくなってショートショットの原因になりますが、逆に高すぎると樹脂がサラサラになりすぎてバリが出たり、ガスが出たりして不具合の元になります。
特にノズル温度は忘れがちですが、過熱しすぎないように注意しましょう。
●吸湿性樹脂は、しっかり乾燥してから使う
ABSやPC(ポリカーボネート)などの吸湿性樹脂は、成形前にしっかり乾燥させることが必須です。
乾燥が甘いと、水分の影響で成形中に加水分解が起き、粘度が下がってバリが出やすくなります。
乾燥の温度や時間は、材料ごとのデータシートを参考に。たとえばABSなら80℃で2〜4時間くらいが目安です。
●材料の“グレード”選びも、バリ対策の一つ
同じ材料でも、グレードによって粘度(流れやすさ)はかなり違います。
たとえば薄肉製品なら流動性の高い(サラサラした)グレードが必要になりますが、肉厚品なら逆に粘度が高め(ドロッとした)グレードのほうが、過充填によるバリを防ぎやすくなることもあります。
もちろん充填不良とのバランスは必要ですが、「フローが良すぎる材料=バリが出やすい」と覚えておくとよいでしょう。
●樹脂の滞留時間をチェックする
シリンダーの中に樹脂が長く居座っていると、分解が進んで粘度が下がってしまいます。
たとえば、ショット量が小さいのにデカい成形機を使っていたり、サイクルタイムが長すぎたりすると、樹脂の“回転率”が悪くなって劣化の原因になります。
必要に応じて、サイクルを短くしたり、計量後にムダな滞留が発生しないように成形条件や段取りを見直すといいです。
●冷却バランスも、見落としちゃいけないポイント
型の冷却がうまくいってないと、一部で樹脂温度が高止まりしてしまい、そこだけ粘度が落ちてバリが出る…なんてことも。
金型の冷却水ラインや冷却回路のバランスが取れているか、全体が均一に冷えているかを確認しましょう。
冷却がしっかりしていれば、充填時の圧力も下げられて、結果的にバリも出にくくなります。
過充填(オーバーパック)とショットサイズの問題
●“過充填(オーバーパック)”は、バリの隠れた原因になりやすい
過充填とは、まだ一部の細かい部分が埋まっていないうちに、すでに満たされた部分に余分な樹脂がどんどん押し込まれてしまう現象です。
射出成形では、太いランナーや肉厚部分など“流れやすい場所”が先に埋まりやすく、そこにどんどん樹脂が入り込んでいくと、まだ埋まっていない他の場所を待っている間に先行部だけが“押されすぎ”状態になります。
この押し込みすぎによって、局所的にものすごく高い圧力がかかり、金型の合わせ面がわずかに開いてしまって、そこからバリが出るわけです。
●特に“複数キャビティ”や“ゲートが複数ある金型”で起こりやすい
たとえば、2個取りの金型などで、片方のキャビティが先に埋まってしまうと、そっちはもう終わってるのに、まだ充填中の反対側に合わせて樹脂が送り込まれ続けます。その間、もう満タンのほうに無理やり樹脂が押し込まれ続けることで、オーバーパック → バリという流れになってしまいます。
●ショットサイズが多すぎるのもNG
樹脂の射出量(ショットサイズ)が多すぎると、それだけで“入りすぎ”になります。たとえ射出圧を下げたとしても、入れすぎてしまった樹脂の逃げ場がなく、型の隙間から無理やり漏れ出してバリになってしまいます。
要するに、「流れやすい場所に入れすぎない」「全部の部分がバランスよく埋まるようにする」ことが重要。過充填は一見わかりにくいですが、バリや型トラブルの元になる厄介な現象なので、ショット量やゲート設計、流動バランスなどをしっかり見直して対策しましょう。
改善策
●ランナー・ゲート設計を見直して、流れを均一にする
複数キャビティや複数ゲートの金型では、どのキャビティにもできるだけ同時に樹脂が行き渡るように設計するのが基本です。
理想は「完全なバランス配置」ですが、実際には難しいことも多いので、ゲート径や絞り(ゲートランド)を微調整して、各キャビティの充填タイミングをそろえる工夫をします。
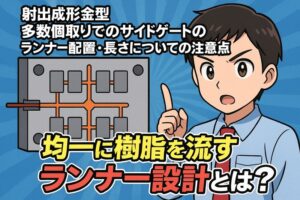
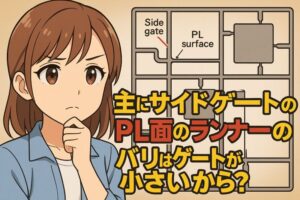
また、大きさの違う製品を1枚の金型に配置する場合は、左右対称に並べるなどしてバランスをとるのがポイント。流れやすい部分と流れにくい部分の偏りをなくせば、特定部位だけに圧力が集中してバリが出る…なんてことを防げます。
●射出から保圧への“切替タイミング”がカギ
射出成形機では、ある程度充填が進むと、自動的に射出(速度制御)から保圧(圧力制御)に切り替わります。
この切替のタイミングが遅すぎて、製品が100%近くまで速度で詰め込まれてしまうと、過充填→バリの原因に。
理想はキャビティが95〜98%くらい充填されたあたりで保圧に移行すること。
逆に切替が早すぎると今度は充填不足になるので、ショット量とのバランスを見ながら細かく調整する必要があります。
●ショット量(計量)も必要最小限に
射出量が多すぎると、それだけで“余った樹脂”が過充填となってバリの原因に。
計量ストロークを少し減らして、必要ギリギリのショット量にしてみましょう。
もしそれでショートショットになってしまう場合は、樹脂温度や射出速度を少し上げて、流動性を確保する方向で調整します。
●サイクルタイムが長すぎてもNG
ショット量は適正でも、成形サイクルが長すぎると、シリンダー内で樹脂が熱を受けすぎて粘度が下がり、結果的に過充填しやすくなることがあります。
冷却時間など、全体の工程を見直して、樹脂が“寝かされすぎない”ようにしましょう。
●保圧プロファイルを“段階的に”調整する
保圧をずっと一定でかけっぱなしにすると、ゲートが固まったあとも無理やり樹脂を押し込んで、バリの原因になります。
これを防ぐには、最初だけ少し高めの保圧をかけて、あとは段階的に減圧していく「マルチステージ保圧」を活用します。
ゲートがシールされたら保圧をゼロにすることで、余分な詰め込みを防ぎ、金型へのストレスも減らせます。
●それでもダメなら、材料グレードの見直しもアリ
すべての調整をしてもどうしてもバリが出るなら、思い切って粘度の高い材料に切り替えるという手もあります。
現在使っている樹脂が“流れやすすぎる”タイプだと、充填完了後もスルスル入ってしまってオーバーパックになりやすいです。
ただし、材料変更は強度や寸法精度に影響する可能性もあるので、テスト成形などで慎重に評価しながら進めてください。
過充填対策は、成形条件だけでなく金型設計や材料選定など、複数の視点からの調整が必要になります。
小さな違いが大きなバリの差につながるので、ひとつひとつ丁寧に見直していくことが大切です。
スプルーブッシュ等の金型部品要因
●意外と見落とされがち?スプルーブッシュが原因のバリ
スプルーブッシュ(射出機ノズルと金型をつなぐ入口の部品)も、実はバリの原因になることがあります。
射出時には、ノズルから大きな圧力がスプルーブッシュにかかりますが、これが金型内部でしっかり支えられていないと、圧力でブッシュがわずかに“押し戻される”ような動きをして、パーティングラインが少しだけ開いてしまうことがあります。
こうなると、ちょうどスプルー周辺やその近くでバリが出る…という現象が起きやすくなります。
ノズルの押し圧は、機種や条件にもよりますが5〜15トンにもなることがあるので、スプルーブッシュの周囲をしっかり構造で支えることがとても重要です。
●ブッシュの長さや位置にも注意!
スプルーブッシュの先端が、金型のPL面より出っ張っていたり、干渉していたりすると、型を閉じたときにその部分で干渉して完全に閉じきれないというトラブルにつながり、そこからバリが出てしまうこともあります。
また、ブッシュと金型の嵌合部に摩耗や段差があると、そのすき間から樹脂が漏れてバリが出るケースもあります。定期的に摩耗チェックと再仕上げをしておきたいポイントです。
●ピンやインサート部の精度も見直しを
さらに見落とされやすいのが、エジェクタピンの周囲にある“クリアランス(すき間)”や、インサート部品同士の合わせ面。
ここがルーズだったり、加工精度が甘いと、そこから局所的に樹脂が漏れてバリになることがあります。
つまり、スプルーブッシュまわりの設計・取り付け・精度管理が甘いと、それだけでバリの原因になってしまいます。スプルー周辺にバリが集中しているようなら、金型構造とブッシュの状態をしっかり見直してみるのがオススメです。ちょっとした“押され”や“出っ張り”が、実は大きな品質不良の引き金になっているかもしれません。
改善策
●スプルーブッシュをしっかり支える構造にする
スプルーブッシュはノズルからの強い押圧を受けるパーツなので、金型設計の時点で、その周囲に肉厚な支持構造や支柱を入れて、押されてもたわまないようにしておくのが鉄則です。
もし既存の金型でブッシュが押され気味な場合は、背面にサポートプレートを追加する改造も有効です。
また、ノズルとブッシュの当たり面に段差や段付きがあると、そこに力が集中して型が傾いたり変形したりする恐れがあるので注意。
ブッシュは“面で押さえる”か、ポケット部にしっかり収まるように仕上げて、圧力を分散できる構造にしておきましょう。
●ブッシュの“出っ張り”には要注意
スプルーブッシュの先端は、型合わせ面より少しだけ奥に引っ込んでいるくらいが理想です。
熱で膨張することも考慮すると、成形時にはピッタリか、ほんの少し引っ込んでいるぐらいがベスト。
もし先端が出っ張っていると、射出時の圧力や熱膨張で金型が“物理的にこじ開けられて”しまい、そこからバリが出ます。
そういうときは、ブッシュ先端を研磨して短くするか、最初から適切な長さのものに交換して対処しましょう。
●摩耗していたら迷わず交換
長く使っていると、スプルーブッシュと金型の嵌合部や、エジェクタピンの穴などが少しずつ摩耗してきます。
たとえばエジェクタピン周辺の隙間が広がると、そこからもバリが出る原因になります。
隙間が0.01mm以上広がっているようなら、オーバーサイズのピンに交換するか、穴を仕上げ直してクリアランスをきっちり戻しましょう。
同様に、ガイドピンやブッシュなどの摩耗でも、型ズレや局所的なスキマが生まれ、これがバリの温床になります。定期点検と交換で防げるトラブルです。
●インサートや可動部の嵌合も見直す
スライドコアやインサートブロックの周辺でバリが出ている場合、そこは嵌合精度やロック機構を再確認しましょう。
スライドコアには、樹脂の圧力で動かないようにしっかりしたロックキーを設けることが大切。ここが甘いと射出圧でズレて、スキマができてバリになります。
さらに、可動ギミックが多い部分では、必要に応じてベントや逃がし形状を追加することで、圧力を逃がしやすくなり、バリ対策にもつながります。
スプルーブッシュまわりは見た目以上に重要なパーツです。ノズル圧のかかり方や取り付けの状態次第で、意外と簡単に型が開いてバリが出てしまうことがあります。
定期的なチェックと丁寧な構造設計で、金型の“入り口部分”からトラブルを防ぎましょう。
バリ防止のための設計・成形条件の最適化
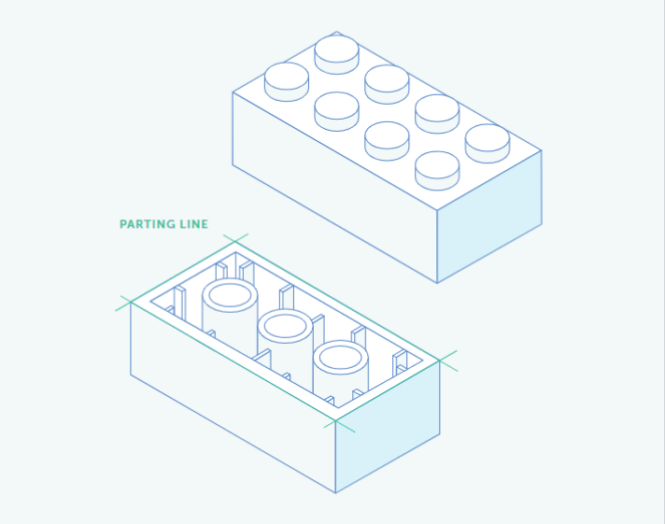
バリ不良を根本から減らすには「初期設計と全体最適」がカギ
バリは一つの原因だけで起きるわけではなく、設計・金型・成形条件・材料・保守と、いくつもの要素が絡み合って発生します。だからこそ、個別の対策だけでなく、最初の段階からバリが出にくいように設計・準備しておくこと(DFM:Design for Manufacturability)が、非常に効果的です。
DFMとは?
「Design for Manufacturability(DFM)」とは、日本語でいうと「製造しやすさを考慮した設計」という意味で、製品の設計段階から「量産のしやすさ」「不良の出にくさ」「コストの低さ」などを意識して設計する考え方です。
【設計段階での工夫】形状・分割位置を考える
バリが出にくい製品形状や金型構造を最初から意識しておくだけでも、後々のトラブルを大幅に減らせます。
たとえば?
- パーティングラインを製品の角やエッジに持ってくる
- 製品の中央にラインが走るような型配置は避ける(バリが目立つ・除去しづらい)
- 複雑すぎる形状や微妙な抜き勾配の不足は、射出圧が高くなりやすくバリの原因に
- 必要なら、フラッシュフリー金型(高精度金型)の導入も検討する
見えにくくなる工夫をするだけで、たとえバリが少し出ても目立たず、機能にも影響しにくくなります。
【CAEシミュレーションで予測】バリが出る前に対策する
今では多くの成形メーカーが、金型設計前に樹脂流動解析(CAE)を活用しています。これにより、
- 圧力が集中する場所
- 空気溜まり(エアトラップ)
- バリの出そうな部位
- ウェルドラインや流れの不均衡
などを事前に見える化し、ゲート位置の調整や構造補強など、設計にフィードバックすることができます。
一部メーカーでは、製品図面や3DデータをもとにDFMレポートを無償提供してくれる場合もあるので、早い段階で相談しておくと効果的です。
しかし、CAEはたしかに便利なツールですが、やっぱり万能というわけではありません。あくまで「参考程度」に使うのが現実的で、結局のところは現場での見極めや調整がいちばん重要だったりします。
【成形条件の最適化】バリを抑える設定を探る
成形条件は少しの違いでバリが出たり出なかったりします。熟練の技術者は、
- できるだけ低圧・低温で成形する
- 過剰な安全マージンを削っていく
- 射出・保圧条件の最適化実験を行う
といった手法で、バリの出ない「ちょうどいいポイント」を見つけます。
たとえば?
- まず高めの射出圧・型締め力で成形
- そこから徐々に条件を下げていき
- ギリギリ良品が出る最小条件を見つける
こうすることで、圧力のかけすぎ・温度の上げすぎを防ぎ、金型寿命も延ばせます。
また、量産中もバリの兆候が見えた時点で早めに対応できるよう、製品の観察とプロセスモニタリングをしっかり行うことが重要です。
【金型メンテナンス】清掃・点検は“毎回やる”前提で
バリを防ぐ最後の砦は、金型のコンディション管理です。
- パーティングラインのゴミや樹脂カスは毎サイクルでも除去する意識
- 摩耗部品の早期交換
- 緩みや傷のチェック
- 表面の小さな圧痕・段差を見逃さない
金型がベストな状態を保てていれば、成形条件も安定し、結果的にバリの発生も抑えられます。
まとめ
射出成形におけるバリの発生は、金型設計、成形条件、材料の状態、機械の調整など、いろんな要因が絡み合って起こります。そのため、完全にゼロにするのは正直簡単ではありません。
でも、ここまで紹介してきたような、金型設計の工夫、条件設定の見直し、材料の管理、こまめな保守点検を組み合わせることで、バリの発生頻度や量をグッと減らすことは十分可能です。
特にABSやPPのような汎用樹脂では、「いかに生産性を落とさずに、バリを減らせるか」というバランスがとても重要になります。バリを抑えることができれば、後工程のバリ取りの手間が減ってコストが下がるだけでなく、製品の外観や精度も格段に良くなります。
つまり、バリの少ない金型設計と成形ができる=高い技術力の証。これはお客様からの信頼にもつながります。
地道なプロセス改善と日々の金型管理の積み重ねが、最終的には「バリの出ない安定成形」につながっていきます。目に見えない努力の積み重ねこそが、成形品質を支える力です。これからも着実に、一歩ずつ改善を重ねていきましょう。
リアクション投稿