金型のインローとは?
今回は金型のインローについてです。
「インロー」というのはPL面や各種合わせ面での位置決め、ズレ止めの意味で使われます。
例えばキャビ入れ子とコア入れ子にそれぞれ出っ張りと凹みをつくりお互いにテーパで合わせるといった感じですね。
簡単な構造でいえば次のような図になります。
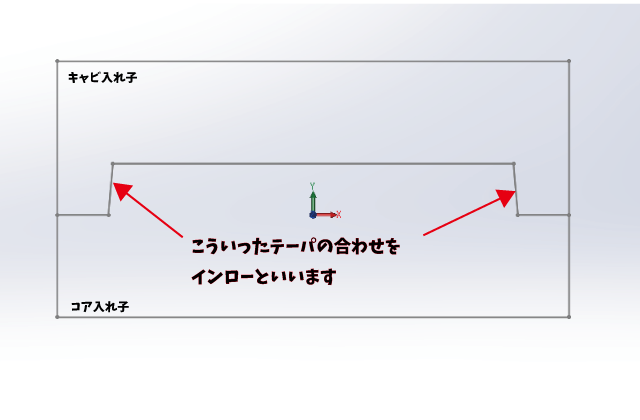
インローは上下にテーパで合わせるのが基本です
インローのメリット
ここでインローをつけるメリット(役割を含む)を挙げていきたいと思います。
インローのメリット
- キャビコアのズレを防止出来る
- ピンなど細長い形状のものの合わせにもがっちり合わせられる
- 樹脂圧による倒れを防止出来る(偏肉対策)
- キャビコアに円状の形状など半々に加工したときにミガキが楽になる上継ぎ目がきちんと合わせられる
- ロッキングブロックの倒れ防止
- 樹脂圧による横方向への開きの防止
ほかにもあるかもしれませんが
ざっと挙げるだけでもこれぐらいはあり、意外と使う機会は多いです。
金型設計をする上での基本ともいえますね。
入れ子のインロー例
金型の入れ子にはよくこんな形状があると思います。これはインローを4隅につけたもので、この中央部に製品部が加工されている状態。この形状でしたら上下左右に合わせがズレることはないですね。
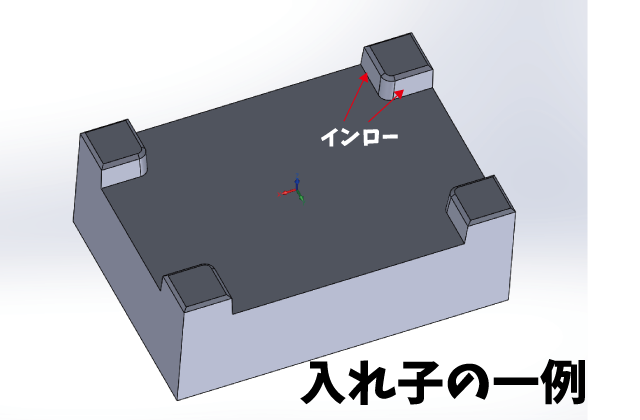
入れ子の四隅にインロー
キャビコア入れ子の合わせ確認もいちいちモールドベースに入れることなく出来るので楽になります。
続いてピン形状のインローです。
ピンのインロー
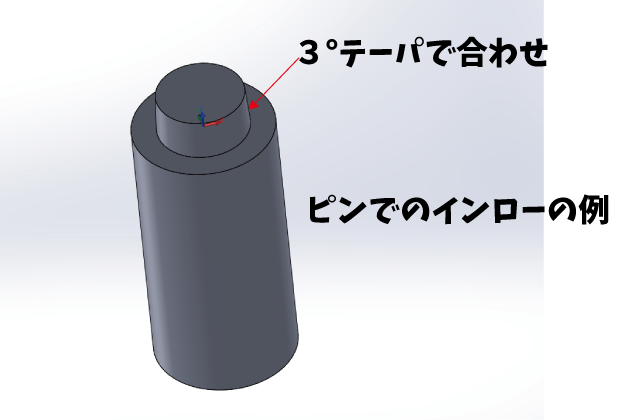
簡単ではありますが、こういうインローがあれば樹脂圧によるズレも起きません
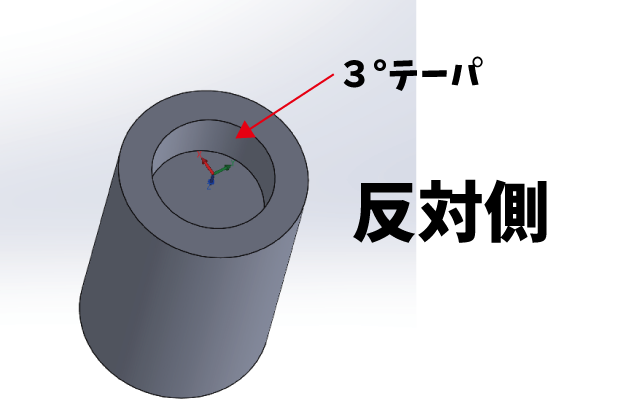
反対側です
ピン形状の製品の場合は太さや長さにもよりますけどなければ危ない場合があります。
場所によってはピンが樹脂圧で曲がったり、合わせ面がズレて偏肉になったりしてまともな製品になってくれません。
入れ子のインロー例2
前述したメリットにも挙げましたが、
キャビコア入れ子に円など同形状の加工をしたときの例がこちらです。
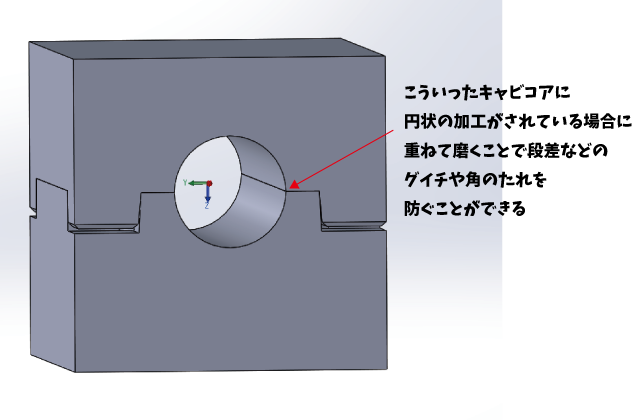
キャビコア入れ子に同形状の加工がされている場合
特に円系の形状の場合、キャビ・コア別々に磨いてしまうとPL面角部がたれてしまい(角がとれてしまう)バリやグイチに見える原因になりがちです。(グイチとはズレのことです)
そうしたトラブルも、インローを設けることで、合わせて一緒に磨く事できれいな形状を維持できるようになります。
また、キャビとコアの製品部がグイチかどうかの確認にも使えるので、多少ずれていた場合はこの合わせた状態で一緒に磨いてしまえば段差のないきれいな円にすることが出来ます。
ちなみにキャビコア製品部のズレ(段差)といってもおそらく0.01mm~0.02mm程度かと思われますが、それでも指で触ると若干の段差が意外とわかってしまうもので、製品外観にも表れてしまいます。
まとめ
インローというのは、簡単にいえば「ズレ止め」「位置決め」です。これにより様々なメリットがあることは上述したとおりで高さのあるコアの場合は倒れを防ぐこともできるため偏肉防止の対策にもなります。
金型の設計をするうえであらゆる面で使えることから設計にはなくてはならないものですし、上述もしましたが、磨き用途やキャビコア合わせて加工したい場合、スライドを重ねて加工したい場合などに備えて、あらかじめ入れ子やスライドに相向かいにインローをつけることもあります。
また例外として通常のインローとは違いますが、スライドのテーパが金型正面から見て4方向にある場合などはそれがインローの役目をすることがあります。例えば3方向のスライドであってもそれが2個取り、4個取りなどで上下左右にテーパがあればそれがインローの役目になるということです。
ということで、今回はインローの役割やメリットについてを書いていきましたが、次回はもう少し突っ込んだインローの内容にしてみます。
インロー関連としてこちらもどうぞ
PL(パーティングライン)をモールドベース全面にするのはNG