製品の形状や金型の大きさによってはインローの構造がまるで意味をなさない場合があります。
一見正しいと思われる構造でもインローになっていない構造とはいったいどういうものなのでしょうか?
ということで今回はそのインローになっているようでなっていないNG例を1つ挙げてみたいと思います。
こんなインローは意味がない?
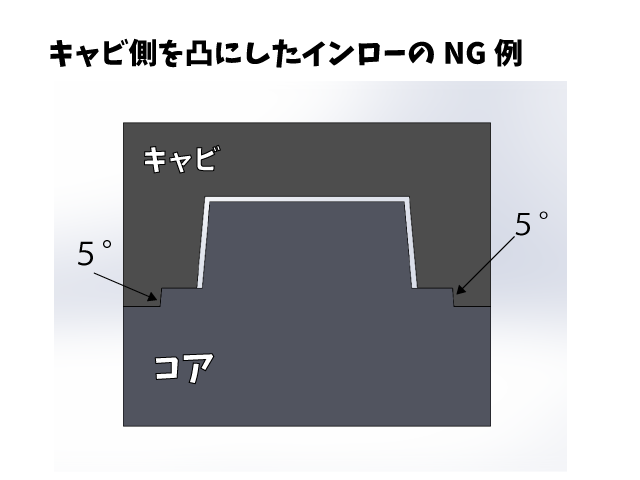
キャビ(固定側)を凸(受け)にしたインロー。 今回はモールドベース全周にインローが付いたパターンです。
上の図はキャビとコアの断面で、キャビ側を凸にしたインロー構造を表しています。
製品が高さのある箱状で、
インローがモールドベース全周についているものと仮定します。
一見良いように見えるこのインロー構造なのですが、実はNGなんですよね。
さて、どこがNGなのでしょうか?
なぜにこの構造はNGなのか?
NGの理由は以下の図でご説明いたします。
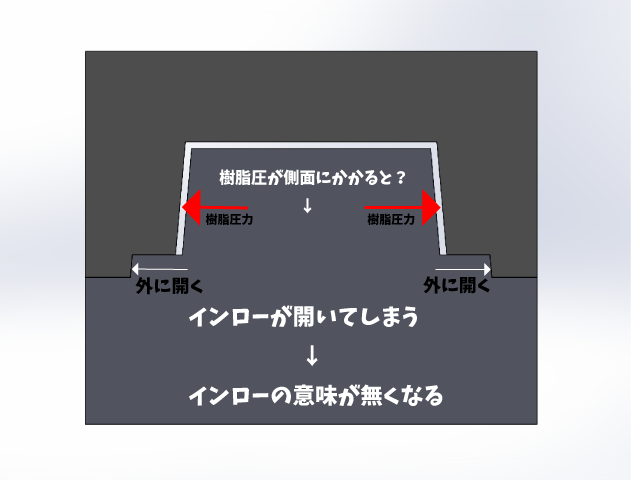
樹脂圧(力の向き)が外側にかかるためキャビは開いてしまう→インローの意味無し
キャビ側製品部に成形時に樹脂が流れると、樹脂の圧力が外側に働き、
キャビが外に開こうとしてしまいます。
そうなってしまうとがっちり嵌まっていたインローが外側に流れてしまうので
インローの意味がなくなり、
バリ、グイチ、偏肉など製品によって様々なトラブルが発生してしまいます。
このままでは不良品が出来てしまうので
インロー構造の変更をしなければいけません。
正しいインロー構造は?
では、インロー構造をどう変更すれば改善されるか?ということですが、
一つ目は以下の図のように凸をコア側にもってくることでクリアできます。

凸をコア側(つまり反対)にして型の開きを防止
可動側(コア)が外にくることで、キャビに外向きに樹脂圧がかかっても
コア側でしっかりと開き防止として受け止めてくれるので外に開くことを防ぐことができるというわけです。
続いてもう一つの対策として、インローを溝状にする方法もあります。
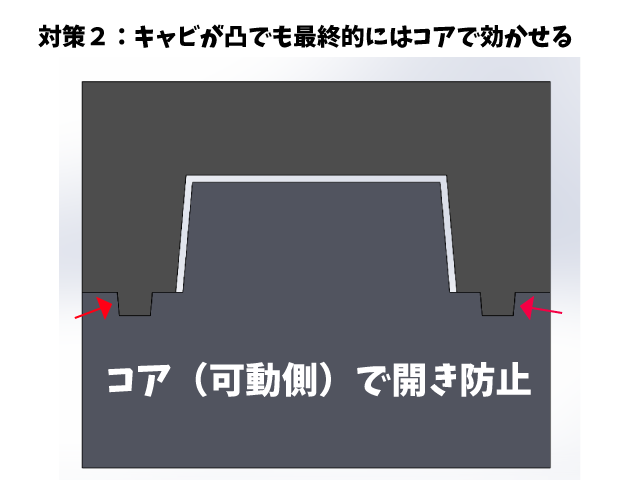
キャビが凸でもインローを溝のようにし、最終的にはコア側で開きを防止させる
こちらはキャビが凸でもコアが凸でも両方ともがっちり効きますのでどちらでも構いません。
溝はあまりにも薄いと効果が無いのでそこそこの厚さと高さは必要になります。
(比率的に大体上の図くらいはいりますね。あくまで大体ですが)
まとめ
ではまとめです。
- キャビをインロー外側にもってくると金型が樹脂の圧力で外側に開いてしまう
- 対策はコア側を開き防止のため外側からインローで受け止めるように変更する
製品の形状、大きさ、高さなどにもよるので一概にすべてのインロー構造に当てはまるわけではないですが、
樹脂の力がどう加わるのか?を考えれば自然と最初のNG例はダメだということに気付けるかなと思います。
今回は単純な製品形状での例でしたが、複雑な形状だとこういったケースで、ついうっかり
金型を製作してしまい、「バリ」が直らない原因になっててしかも気付かない・・・
なんてことがあるかもしれません。
またインローだけでなく、テーパー形状のついたロッキングブロックやスライドなども含めて同じ意味で
当てはまってくるケースもあるかと思います。(要はテーパ部の受ける側が力不足になってないかってこと)
注意して設計したいものですね。
関連記事
リアクション投稿
コメント一覧 (2件)
[…] やってはいけない!?インローのNG例 […]
[…] やってはいけない!?インローのNG例 […]