前回の続き
金型のインローの構造、意味、役割について injection Molding
今回は、スライドが縦長になっている場合の例を出したいと思います。
キャビ側にロッキングブロック、コア側にスライドという型構造です。
ロッキングブロックとインロー
まずはこの製品から考えていきたいと思います。
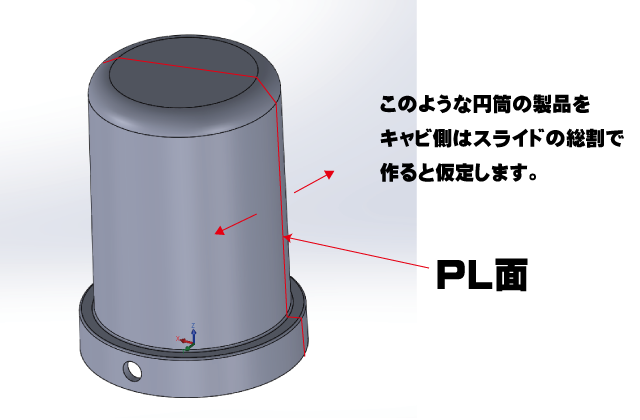
赤線がPL面(スライド割面)です
そこそこ縦長の円筒で
根本に5mmのピンがついているのでスライドで総割りする(ちょっと無理矢理です)という前提でいきます。
赤い線がPL面(スライドの割面)でピンが抜ける方向に抜いていくという構造ですね。
この製品のキャビ側になるスライドを作るとこんな感じになります。
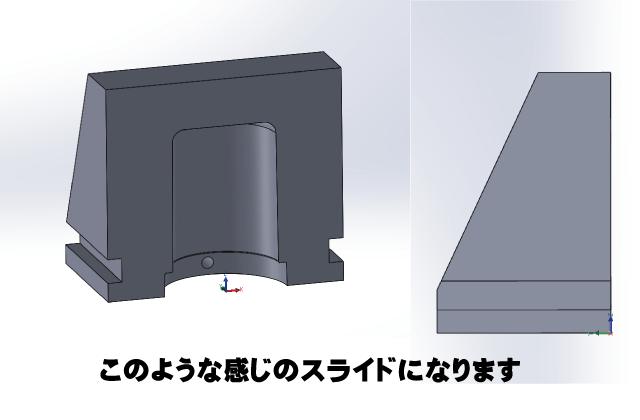
縦長のスライドです
(ゲートがないとか、こまかいことは抜きにしてください)
型構造
このスライドにロッキングをあてると?
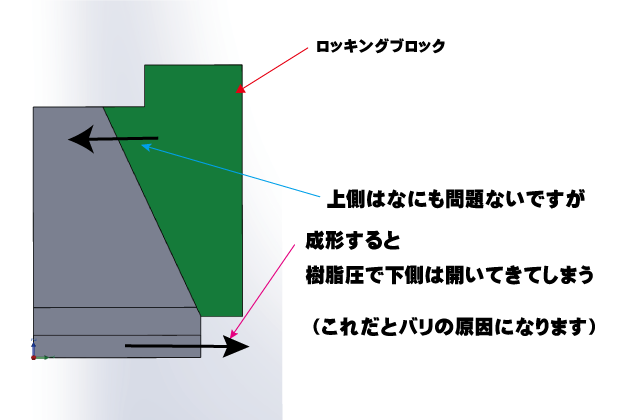
ロッキングのダメな例
緑色がロッキングブロックです。
スライドが縦に長いせいで、これだと成形の際に樹脂圧に負けて
下側がひらく可能性があります。
これはロッキングブロックが、固定ベースに締め付けされている根本は強いですが、
先端にいくにつれて支える力が弱くなることが原因です。
スライドが開いてしまうと、当然ながらその部分がバリとなり
不良品を出してしまうことになってしまいます。
解決方法
解決方法は
可動側のストリッパープレート、もしくは可動ベースに
インローを作り、
ロッキングブロックにも同様の形状にさせて
可動側でスライドが開かないように「受け」を作れば良いんです。
図でみるとこのような感じです。
このようにすると、スライドの下側までしっかりと
可動側で支えられるのでスライドが開いてしまうのを防ぐことが出来ます。
出来れば図には見えてないですが、ロッキングブロックは左右方向もニガシをつけず
がっちりとインローをつけることをオススメします。
スライド側だけは力がかからないので可動のスライド側はニガシても大丈夫です。
まとめ
今の金型はおそらく大体はこのような型構造になっていると思われますが、
20年かそれ以上昔の金型だとちょっとその辺甘いものもあったりします。
インローは主に位置決めのように思われがちですが、
射出成形金型の場合は樹脂の圧力に負けないように定位置で支えるという意味もあります。
そのほかの例を挙げるとすると、
端っこに片割れを起こしてしまった製品部に
テーパで入れ子をつくってそこに隣接するようにいれて補強し、それ以上の割れを防ぐという
利用方法もあったりします。(あまり使いませんけどね・・・)
リアクション投稿
コメント一覧 (1件)
[…] ロッキングブロックでのインローの利用例 射出成形金型 […]