ゲートとは
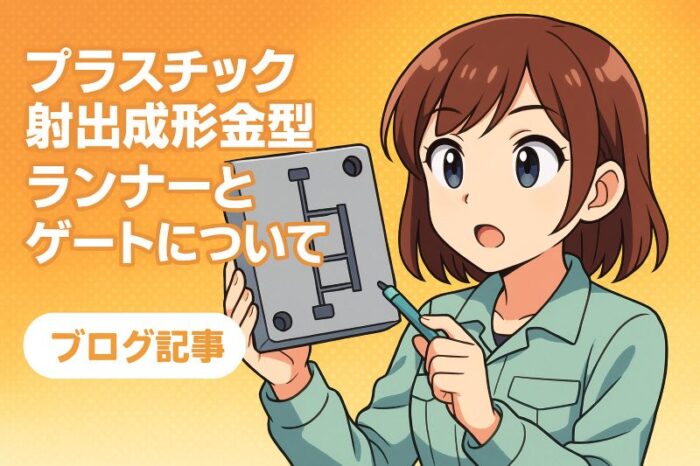
ゲートとは成形機から金型の製品まで、樹脂を到達させる際に必要な経路のことです。
代表的なゲートとしては4種類あり、製品の種類やそれにまつわる様々な目的、金型構造などを考慮して決められます。
- サイドゲート
- サブマリンゲート
- ピンポイントゲート
- ダイレクトゲート
ゲートの役割
ゲートにはいろいろな役割があり、
それなりの意味があっての構造となっています。
- 樹脂が製品部に入るまでの速度や方向の制御
- 樹脂流入後にゲート部のほうが先に固まることでの逆流や圧力の調整
- 狭いゲートを抜ける時の摩擦熱により発熱させ樹脂の流れをより容易にさせる
- ゲートの最終地点を細くすることで製品との切断を容易に出来る
基本的にはダイレクトゲート以外のゲート方法は
製品とランナーの間の部分は、従来よりも狭く細くする必要があります。
この部分を「ランド」と呼びます。
ランドの幅や深さは製品により異なりますが
ランナーの幅が6ミリで深さ5ミリだった場合、ランドの大きさは幅3ミリ深さ1.5ミリといった具合です。
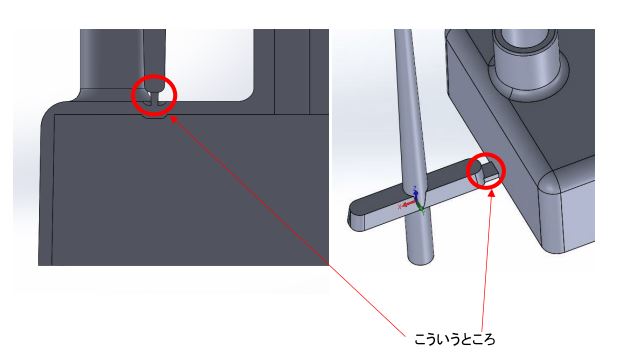
ランドには製品とゲートを切断する際の痕を残さない、もしくは目立たなくさせるためという意味もあります。
ランドの長さ(ランナーと製品との距離)はおよそ2~3ミリ程度が一般的です。
また多くの場合
ランド部分にはランナーから製品部に向けてテーパーをいくらかつけます。
これはランナーからの樹脂の流れをよくするためです。
ゲート位置はどこでも良いわけではない
外観を極力損なわないようにするためにはどの位置にゲートを持ってくるかや
ゲートの大きさ、バランスなどで製品の外観や寸法精度に影響が出るため
金型の設計前の打ち合わせが重要になります。
では、これから紹介するゲートの種類のほうで詳しく解説していきたいと思います。
1.サイドゲート
サイドゲートはもっとも一般的なゲート方法であり
誰もが見たことがあるであろう「プラモデル」はほぼ全てこれですね。
サイドゲートという名の通り、製品の横から樹脂を流します。
多数個取りに利用しやすくコスト的にも一番安く上がるのですが、外観の一部が損なわれることやゲート切断の手間がかかってしまうというデメリットがあります。
また外観を損なわないために、製品の下から潜らせる様に入れるサイドゲートで「ジャンプゲート(バナナゲート)」という仕様もあります。
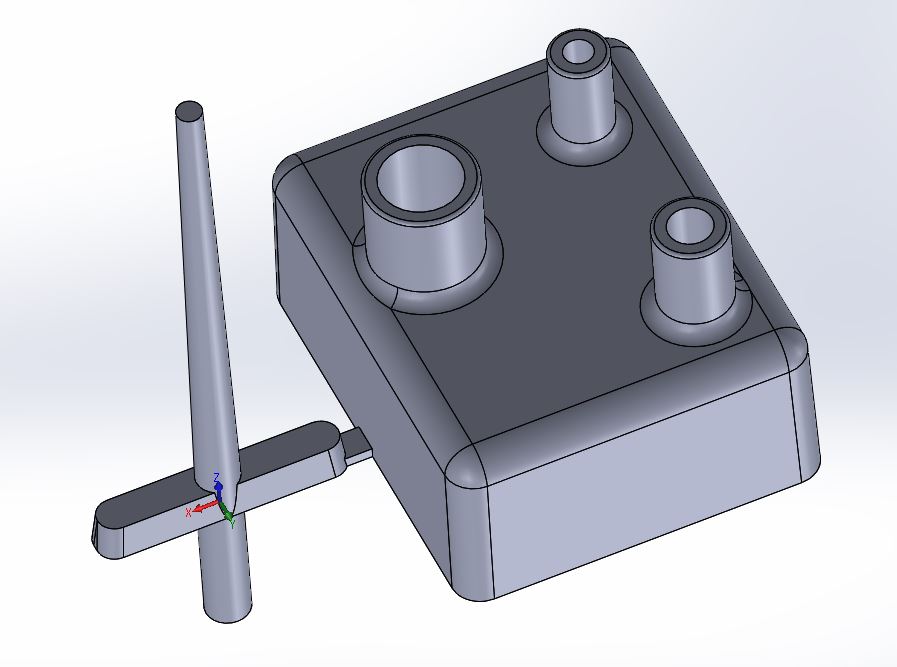
サイドゲートはほぼすべての樹脂に対応できます。
金型が8個取り、16個取りなど複数個取りの場合は
樹脂が均一に入るタイミングを考慮し、ランナーを作らなければいけません。
似た方法でタブゲートというのもあります。タブゲートは流動性の悪い樹脂に有効であり、ジェッティングやフローマークの防止、またゲート付近の残留応力防止にも効果があります。
タブゲートの形状としましてはランナーの途中で一度ランナーを絞る形(串にささった団子?のようなイメージ)で、再びランナーの大きさに戻して最終的にランドから製品へというイメージになります。
あまり利用することはない方法ですが、そういったトラブルになった場合に適用することがあります。
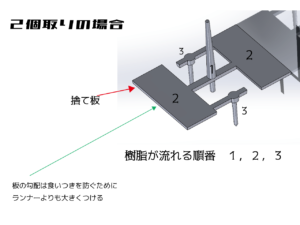
2.サブマリンゲート
続いてサブマリンゲートです。別名トンネルゲートとも呼ばれます。
その名の通り製品の下に潜り込んで樹脂を流す方法です。
特徴として、成形品とゲートを自動切断できるので、サイドゲートと違い成形後の手間を省くことができます。
デメリットとして、複数取りの場合のバランスの難しさがあったり、流動性の悪い樹脂やガラス入りの樹脂には向いておりません。
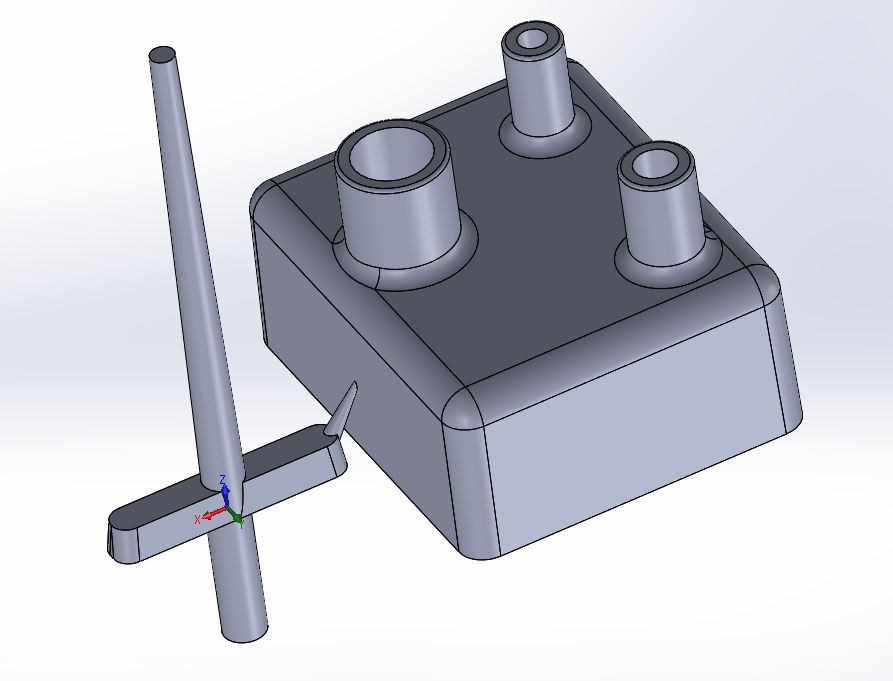
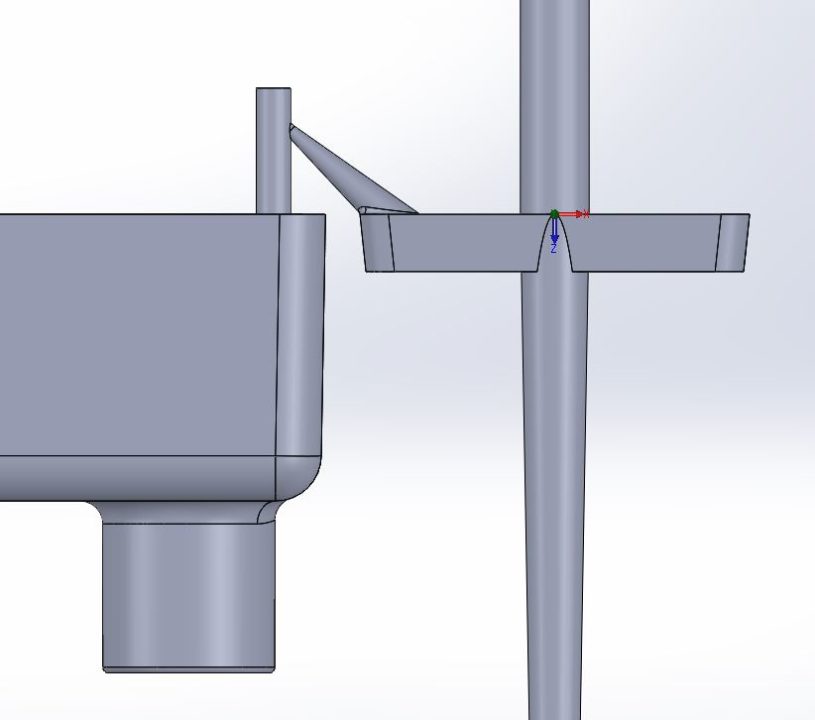
上の図のように意匠面にゲート痕が残ってはいけない場合などには
ランナー近くのコア側に敢えてピンをたてて、そこにサブマリンゲートで樹脂を流し
成形後にそのピン形状の樹脂だけカットするといった方法もあります。
重要!
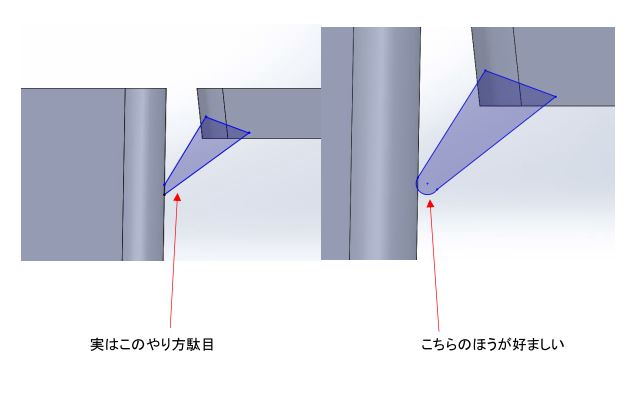
上の図を見てなにが違うのか?ですが
弊社に修理に来られる他社様の金型のサブマリンゲートでは左の図のように製品まで突き抜けるような形状になっているものが実は大変多く見受けられます。
この形状だと製品が取り出される際にゲートかすが擦れて出てきたり、それが次の成形で製品の中に入り込んで製品を傷つけたり、意匠面にポツポツ出たりと悪さをしてしまいます。
ゲートと製品部の穴形状が縦長の楕円となって、断面形状が大きくなりすぎることにより切断され辛くなることから樹脂の切れが悪くなることが原因です。
こうならないための方法ですが、加工の際に右のように角度を変えて、R形状で製品に接するようにすることでこの問題は解消されます。
ゲートと製品との境目の鋭利になった部分に、少しばかりRをつけられるとより良いです。
(ただ、左の形状であっても何も問題が起こらないのであれば全く問題ありません)
3.ピンゲート(ピンポイントゲート)
ピンゲートの特徴は多点ゲートが可能で、複数個取りにも対応可能であり、製品にゲート痕がほとんど残らず、型が開くと同時に製品と分離されるため切断の手間も無いところです。
ただし、アクリルなど流動性の悪い樹脂にはあまり向いておりません。
またピンポイントゲートですと、金型は3プレートタイプになりますのでコストは上がります。
下図2枚目のように
ゲート部にはキャビ側に凹みをつくり、ゲート痕が製品に出ないようにすることが必要なのと
コア側も流動性確保の意味もあって同じ肉厚になるようにたまりをつくる必要があります。
(ただし製品によっては敢えてやらない(もしくは出来ない)場合もあります)
ピンポイントゲートは、利便性の高い方法ではあるのですが
多点ゲートの位置やバランス、圧力の関係で製品へ様々な影響があったりで
実はトラブルの最も多い方法でもあるのです。
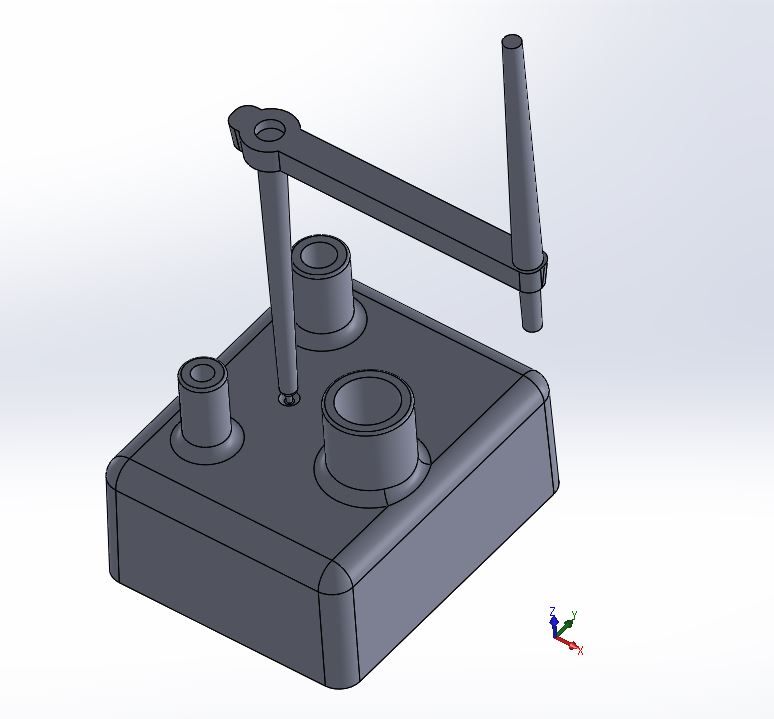
このピンゲートもサイドゲート同様、多点ゲートであったり、複数個取りの場合は樹脂の入るタイミングを考慮して、ランナーを設計する必要があります。
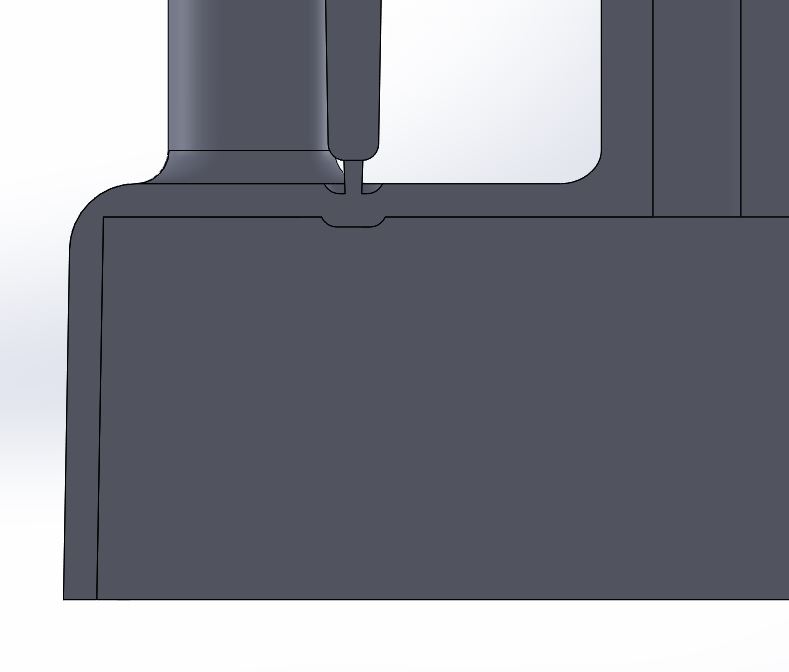
ピンポイントゲートの金型構造についてはこちらから。
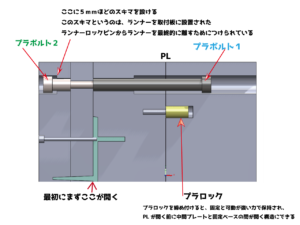
4.ダイレクトゲート
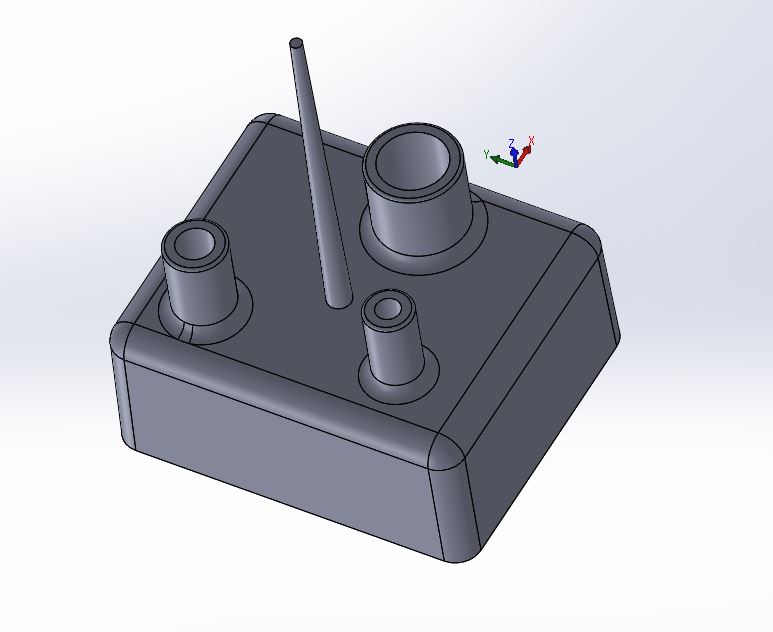
ダイレクトゲートとは、ダイレクトという名前の通り、スプルーブッシュから直接製品へ樹脂を流し込む方法です。
1個取り限定で比較的大きな製品に用いられます。
圧力がかかりやすくゲートの直径が大きい場合樹脂が固化しなかったりゲート付近が高密度になり、残留応力が生じ易く割れや変形が起こるデメリットがあります。
また当然ながらゲートの切断が必要ですが、型構造としてはもっとも単純です。
非制限ゲートと呼ばれるのはこのダイレクトゲートのみとなります。
以上、もっとも一般的に使われるゲート(サイド、サブマリン、ピンポイント、ダイレクト)についてでした。
他にも数種類ゲート方法はあります
今回ここでは紹介しきれませんが、
- フィルムゲート
- バナナゲート
- タブゲート
など、弊社では滅多に使いませんがこれらの方法、また応用した方法があります。
それはまた機会があれば書きたいと思います。
関連記事
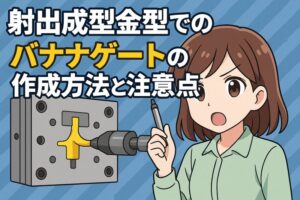
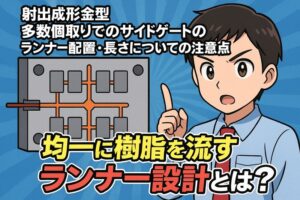
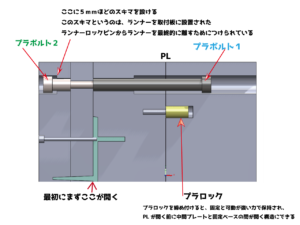
リアクション投稿
コメント一覧 (4件)
[…] プラスチック射出成形金型 ランナーとゲートについて Injection Molding […]
[…] プラスチック射出成形金型 ランナーとゲートについて Injection Molding […]
[…] 関連記事プラスチック射出成形金型 ランナーとゲートについて Injection Molding […]
[…] 関連記事プラスチック射出成形金型 ランナーとゲートについて Injection Molding […]