以前インローの構造、意味、役割についてなどを書きました。
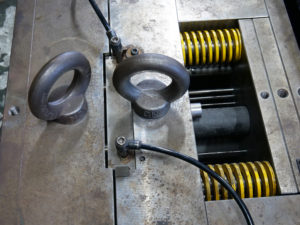
インローは便利な構造ではあるのですが、
とにかくどんな金型にもがあれば良い!(あったほうが良い)というわけではなく、
当然ながら必要のない金型も沢山あります。
やる必要がないのにやるというのは時間、コスト、労力の無駄ですよね。
しかし、必ず必要になる製品(形状)というものもあるんです。
そこで今回はインローを必ずつけるべき形状を2つほど例に出して
書いてみたいと思います。
インローを付けるべき製品とは?
ここで以前書いたインローの記事から
インローの役割について少しおさらいします。
インローのメリット
キャビコアのズレを防止出来る
ピンなど細長い形状のものの合わせにもがっちり合わせられる
樹脂圧による倒れを防止出来る
キャビコアに円状の形状など半々に加工したときにミガキが楽になる上継ぎ目がきちんと合わせられる
ロッキングブロックの倒れ防止
樹脂圧による片開きの防止
以上がざっとインローのメリットを並べたものですが、
射出成型金型でのトラブルの一例として、肉厚が均一にならず
平均2mmでなければならないものが、
片側1.2mm、反対のもう片側が2.8mmになるという偏肉というものがあります。
この偏肉を直すには、インローをつけることで解決することができます。
例えば円形状の製品
さて、ではどのような製品の場合にインローが必須なのかということですが、
円形状の製品の場合です。
例なのでかなり簡単に書きましたが、このような形状の場合
ピンゲート3点、もしくは4点であっても樹脂が均等にまわる保証はないため、
パーティングラインにインローが無ければ偏肉になる可能性が極めて高いです。
サイドゲートやサブマリンゲートでも同様といえます。
円形状の場合のインロー
では、円形状の場合のインローの例を図にしてみます。
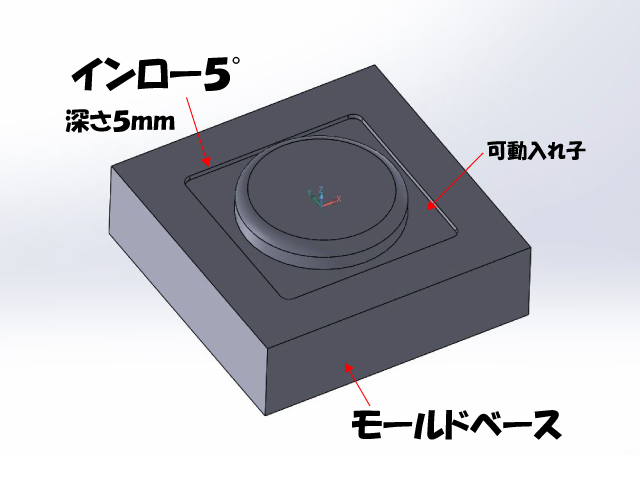
モールドベースにインローをつける
可動入れ子のポケットを5ミリ深く切削し、上側に5°のインローをつけます。
逆に固定側の入れ子はあえて5ミリ長い突き出た入れ子にし、
そこに5°をつけて可動と合わせるといった感じです。
5°という角度はあくまで例で、
インローはものによりますが大体2°~7°くらいの角度にする場合が多いです。
上の図のようにパーティングラインを合わせれば、上下左右にズレることがなくなりますので
偏肉の心配はなくなるはずです。
円筒状の形状にもインローは必要
インロー必須の製品形状としてもう一つ書きたいと思います。
それは、円筒の製品です。
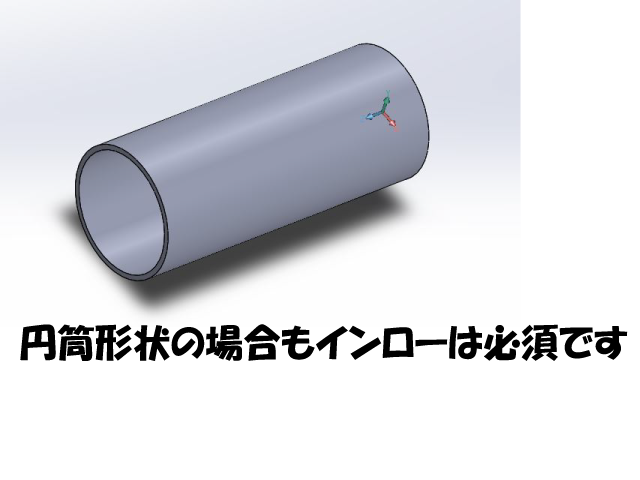
例えばこんな製品です
円筒の場合のインロー構造は?
円筒の場合のインローはよくあるこんな感じです。
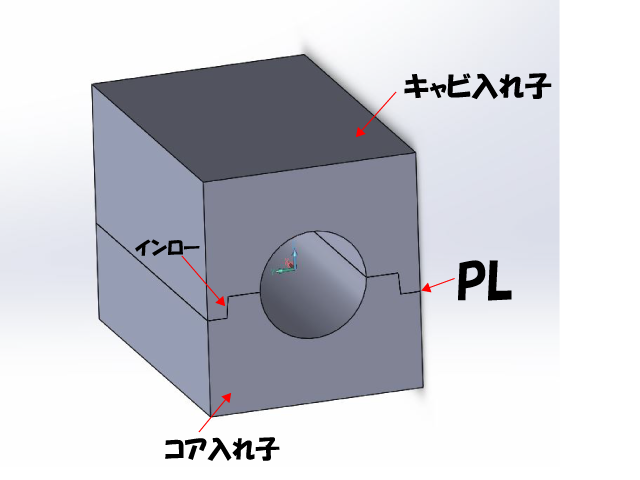
インローは5°です
この場合のインローのメリットは
まず、偏肉を防ぐこともそうですが、合わせが確認しやすいこと、
以前も書きましたが、円形状で磨くことが可能になるので、
成形してからPLに段差が出来るトラブルも解消できるところです。
こういった半円を別々に磨くと、どうしても角がたれてしまったり、
固定と可動で正確に切削していても0.01mm~0.02mmほどずれていて
成形するとPLに線が一本入るだけでなく、それがグイチ(形状があっていない)だとみられたり、
微妙な誤差なのにバリが入っていますよと指摘されたりするものです。
あとは、円筒状の場合、コアピンにも当然ながらインローがないと
倒れが発生し、偏肉となってしまいますね。
まとめ
ではまとめに入ります。
-
円形状の製品は偏肉防止にインローが必要
-
円筒状も同様で合わせ、磨きの際にも役に立つ
-
インローの角度は大体5°前後が目安
こんなところです。
ほんの一例ですが、今回はインローが必要な製品を2つ挙げて
書いてみました。
今後もインローの関連記事を書いていきたいと思います。
関連記事
リアクション投稿
コメント一覧 (4件)
[…] 金型でインローを必ずつけるべき形状(製品)とは? […]
[…] 金型でインローを必ずつけるべき形状(製品)とは? […]
[…] 金型でインローを必ずつけるべき形状(製品)とは? […]
[…] 例えばキャビ入れ子とコア… あわせて読みたい 金型でインローを必ずつけるべき形状(製品)とは? 以前インローの構造、意味、役割についてなどを書きました。 […]