1個取り、2個取りの製品でしたら、ランナーやゲートでさほど樹脂のバランスを気にすることはありませんが、
4個取り、8個取りともなると、製品の配置のほかに、どうランナーを設置するかにも気を配る必要が出てきます。
今回はそのような場合のランナーの配置や長さについて良い例、悪い例を出しながら解説していこうと思います。
多数個取りサイドゲートとは?
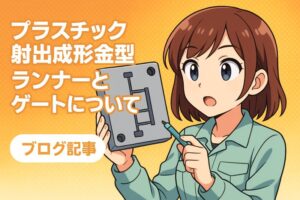
サイドゲートとはその名の通り、製品部の横から樹脂を流し込む最もポピュラーでわかりやすい方法です。(プラモデルが良い例ですね)
2個取りまでなら何も悩むことはありません。
相向かいに2個配置して、ランナーをお互いにふっていけばOKですよね。
しかし、4個や8個になると同じように樹脂が流れていくようにランナーやゲートの設計や調整をしていく必要があります。
なぜなら、同じように樹脂が製品に入らないと品質にばらつきが出たり、バリの原因へと繋がっていってしまうからです。
例えば金型が4個取りだとして、cav1よりもcav4の方が早く樹脂がまわってしまい、cav1まで充填させようとするとPL面が浮いて(型が開いて)cav2,3,4に薄くバリがはってしまう事態になってしまいます。
4個ならともかく、8個ともなると、製品の配置によってはどう修正してもバリが完全に直ることはほぼ無いという事態に陥ることもあり、非常にシビアなところなのです。
ランナー配置NG例
例えば次の図の配置です。
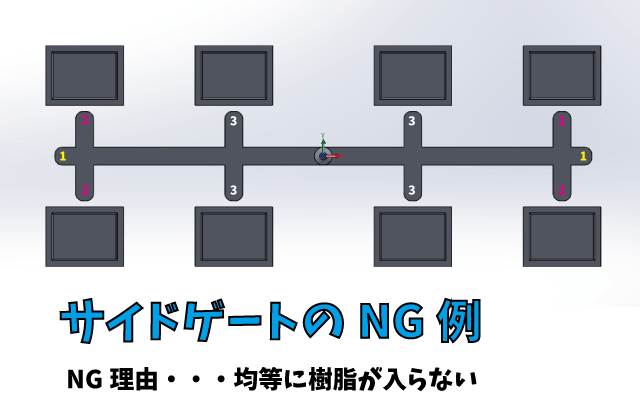
8個取りサイドゲートの配置NG例
番号を振りましたが、このようなランナーの配置だと、端っこの製品4個のほうに先に樹脂が入ってしまい、中4個が遅れて樹脂が入ることになってしまいます。
(樹脂の流れは図のように123の順番で流れていきます)
これでは成形のバランスが悪くなり、端っこ4個にバリが発生したり樹脂圧力で型が浮いてしまったり、各製品の寸法が揃わないなどトラブルだらけでどう対処してもうまくはいきません。
立体で見ると以下のような感じです。
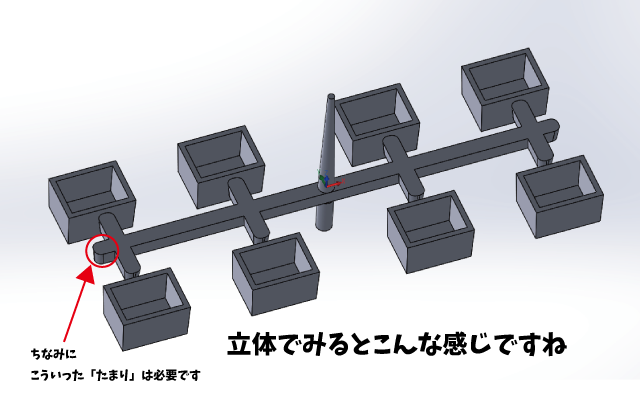
サイドゲートNG例3D
じゃあ、どういう配置にしたらいいのか?
要は「均等」に製品部に樹脂が流れるように、タイミングを同じにすることです。
複数取りランナーの良い例
ではサイドゲートの複数個取りランナーの良い配置例になります。
上のダメな例の金型を修正するとすれば、例えばこんな感じにしてみます。
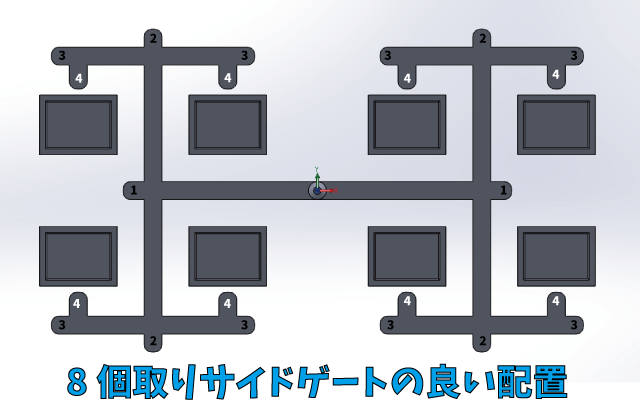
8個取りの良いランナー配置です
1234と樹脂が入るタイミングに番号を振りましたが、この配置ならすべて4のタイミングで樹脂を流すことが出来ます。
上図ではランナーは一旦製品の外側に向かいましたが、下図のように製品と製品の内側にランナーが設置できそうなスペースがあるのであれば、内側から左右にふる形にしたほうが、より樹脂が流れる距離も短くなり良いでしょう。
立体的にみると以下のようになります。
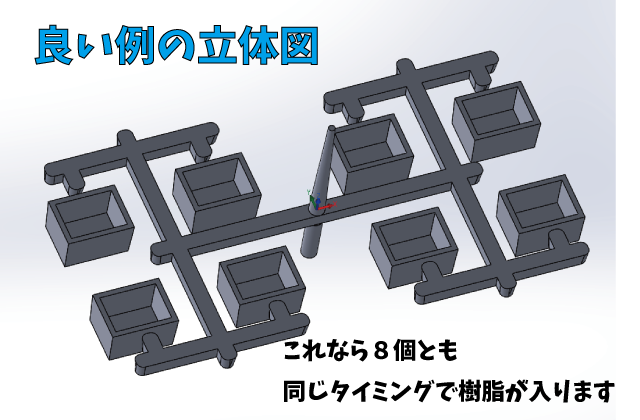
3D図
まとめ:他のゲート方式でも同様?
他のゲート方式でも同様で、サブマリンゲートやピンゲートでも同一の方法で考えるべきです。
サブマリンに関してはサイドゲートと同様の考えで良いですが、ピンゲートではまた違ったバランスを考えなければいけません。
ピンゲートで多点ゲートである場合、それぞれの樹脂が流れるタイミングを考慮していく必要がありますが、
長く高さがある製品だと、ゲートの配置次第では、一方向に早く樹脂が流れてしまうことでコアに倒れが発生し、肉厚2mmの製品であっても、一方の肉厚は1~1.5ミリでその反対方向の肉厚が2.5~3ミリもあるといういわゆる偏肉をおこしてしまう場合があります。
そういった偏肉を防ぐために「インロー」が必要になる場合もありますが、インローに関することは以下のページで。
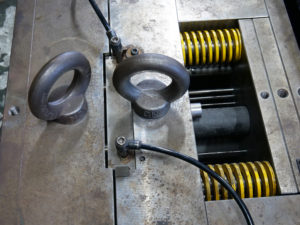
と、ここまで解説してなんですが、8個を均等に樹脂が流れるように設計しても、それだけではまだまだうまくいかないものです。最終的にはショートショットの成形品をいただいて、どこが早く入ってしまうのか、どこが入りづらいのかを判断して、ゲートやランナーを大きくしたり、逆に絞ったり(小さくしたり)して調整をしていかなければいけないのです。これは複数個取り金型の基本ですね。
関連記事
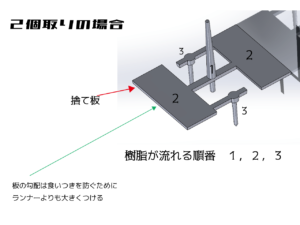
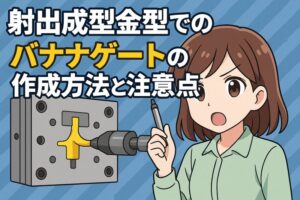
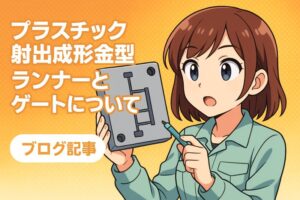
リアクション投稿
コメント一覧 (3件)
[…] 射出成形金型 多数個取りでのサイドゲートのランナー配置、長さについて […]
[…] 射出成形金型 多数個取りでのサイドゲートのランナー配置、長さについて […]
[…] あわせて読みたい 射出成形金型 多数個取りでのサイドゲートのランナー配置、長さについての注意点 均一に樹脂を流すラ… 1個取り、2個取りの製品でしたら、ランナーやゲ […]